Replacing legacy gasket technology to prevent the ingress of oxygen into a vacuum system
A leading chemical manufacturer sought a superior gasket to replace the current semi-metallic gasket utilized throughout this specific vacuum system.
For this system it is crucial to prevent oxygen from entering the vacuum system as it would cause oxidation of the piping contents and compromise the entire batch of chemicals, leading to it being wasted. The DeltaV-Seal, known for its tightness and durability, prevents oxygen from entering the system through the bolted flange joints. This ensures that the product passed through the piping system is not contaminated by oxygen from the bolted flange joints, providing a superior quality end product.
Background
Finding a suitable and cost-effective replacement for the previous specialist vacuum-system gasket was challenging. Therefore, there was a strong desire for a more affordable, tighter, and more durable gasket. Upon learning about the successful use of the DeltaV-Seal in similar plants in the USA and Canada for ethylene service, the European chemical plant decided to conduct further research on the DeltaV-Seal.
The plant owner independently tested the DeltaV-Seal in vacuum conditions to ensure that it could provide a tighter seal compared to their current specialist gasket. The test results showed no leakage from the DeltaV-Seal, leading to its technical acceptance and availability for use in the desired system.
Industry Challenges
With the cost of feedstock and energy having increased significantly, reducing waste and ensuring every batch meets its quality requirements is beneficial in ensuring a competitive margin for the business. The DeltaV-Seal providing such a tight and durable seal ensures that the batches produced are not contaminated by oxygen, this reduces costs and wastage - increasing the profitability of the chemical plant.
DeltaV-Seal effective sealing in vacuum service
All gaskets leak, some significantly more than others. In some industries this leakage is tolerated, while in other applications significantly reducing gasket leakage can have an extremely positive impact on a products quality while reducing waste. The chemical company in this case study had already tested and become comfortable utilizing the DeltaV-Seal on ethylene systems in a sister facility, and following testing have now implemented the DeltaV-Seal on vacuum systems.
By switching from legacy semi-metallic gasket technology, to the DeltaV-Seal, a metal-to-metal seal, the operator is certain there will not be ingress of oxygen into their systems and the quality of the project produced will not be impacted by lesser quality gaskets.
A simple switch from one gasket technology to another, has reduced costs, increased time between planned maintenance, and will ensure the product produced always meets the specified quality criteria.
Solutions
Metal-to-metal seals are proven to be tight and durable for decades. The DeltaV-Seal has been expertly engineered, independently tested, and is precision machined to provide the tightness and durability of a metal-to-metal seal, with the ease of use and installation of traditional semi-metallic gaskets.
In this specific case the Oxygen was successfully prevented from entering a vacuum system through the bolted flange joint. The chemical plants operations team have confirmed the system is oxygen free, and the operator will continue to adopt the DeltaV-Seal on vacuum systems.
Download the full case study
Download the case study by clicking the link below:
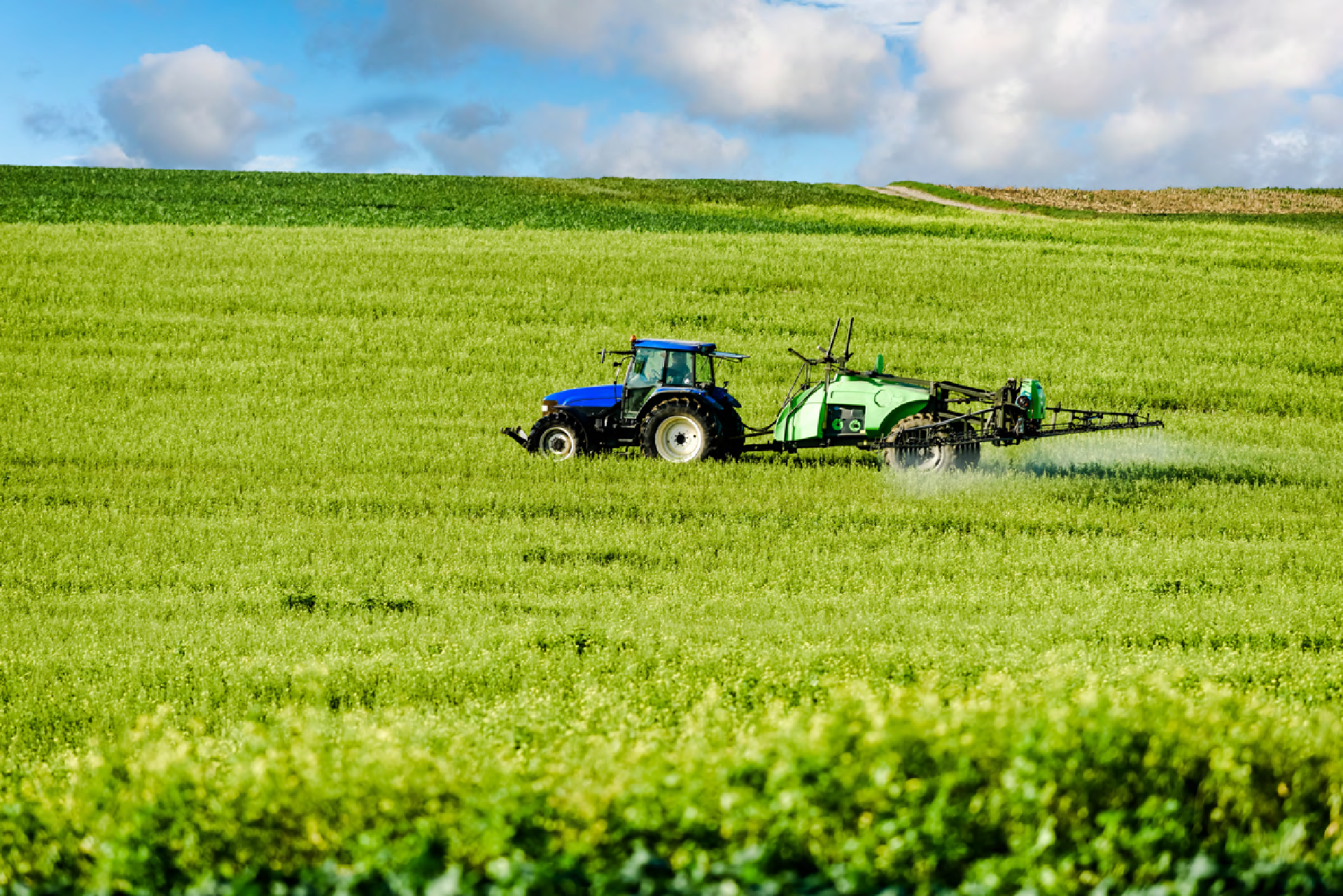
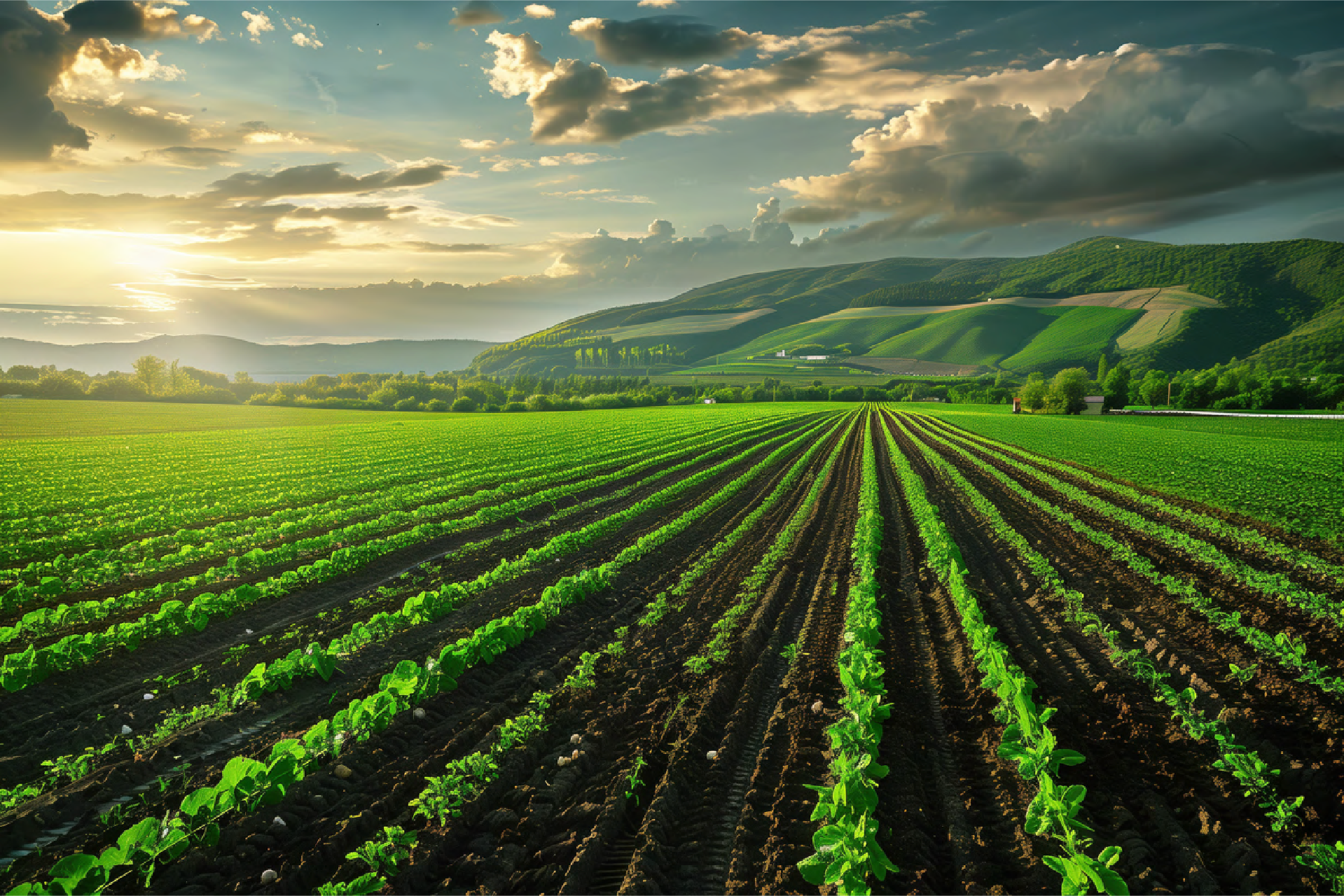
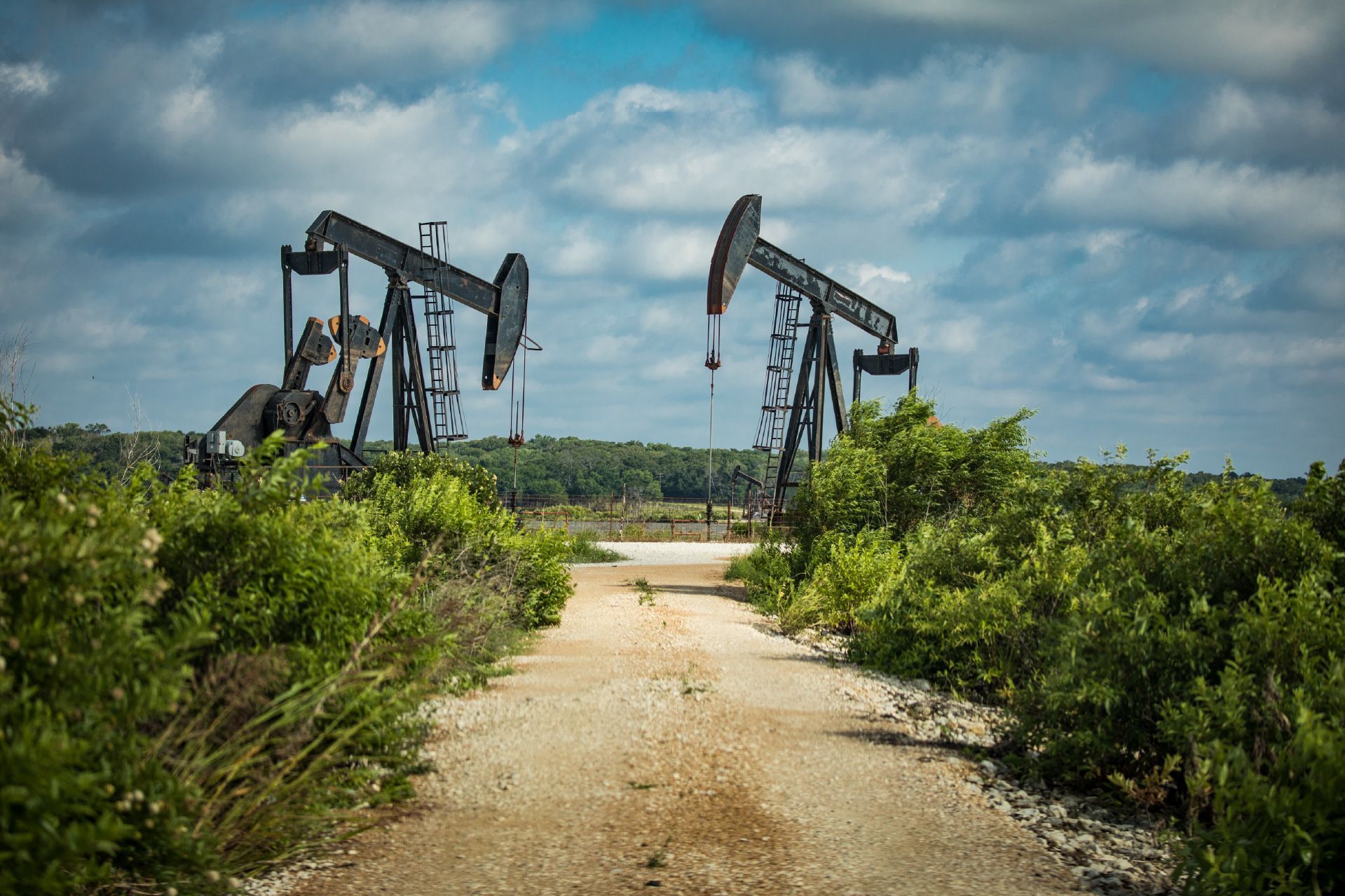
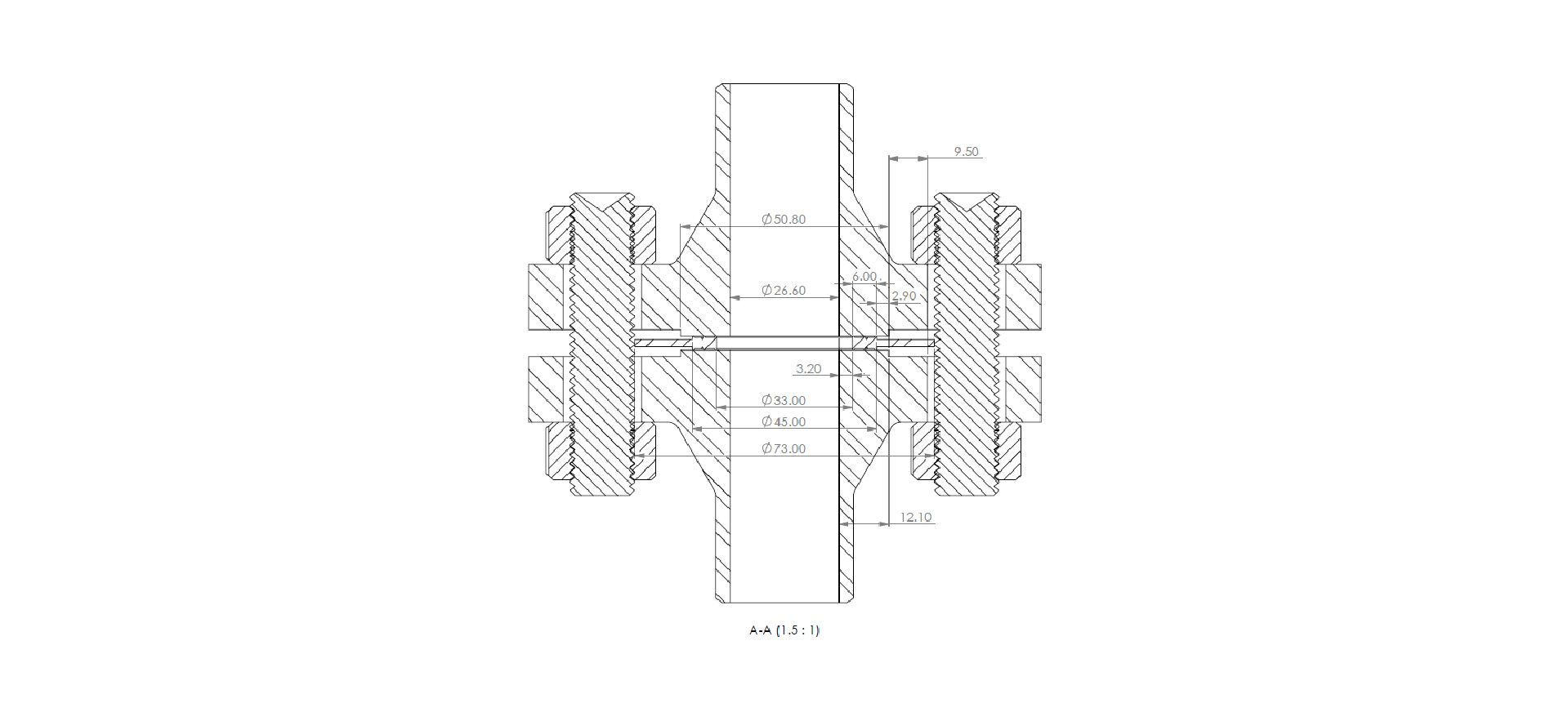
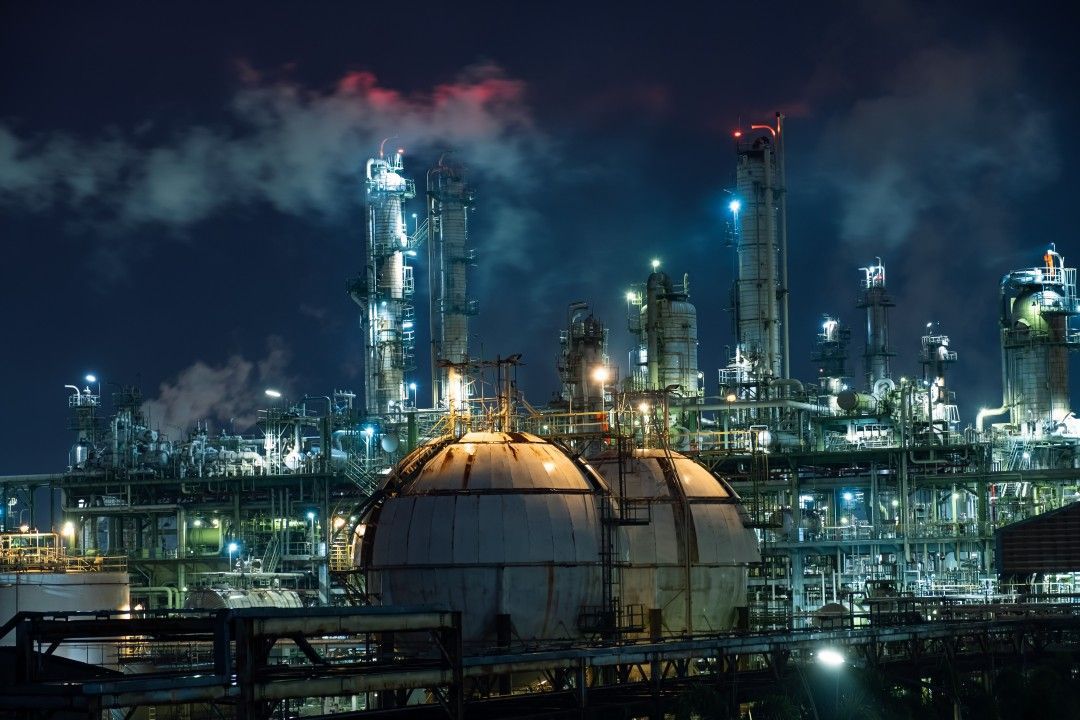