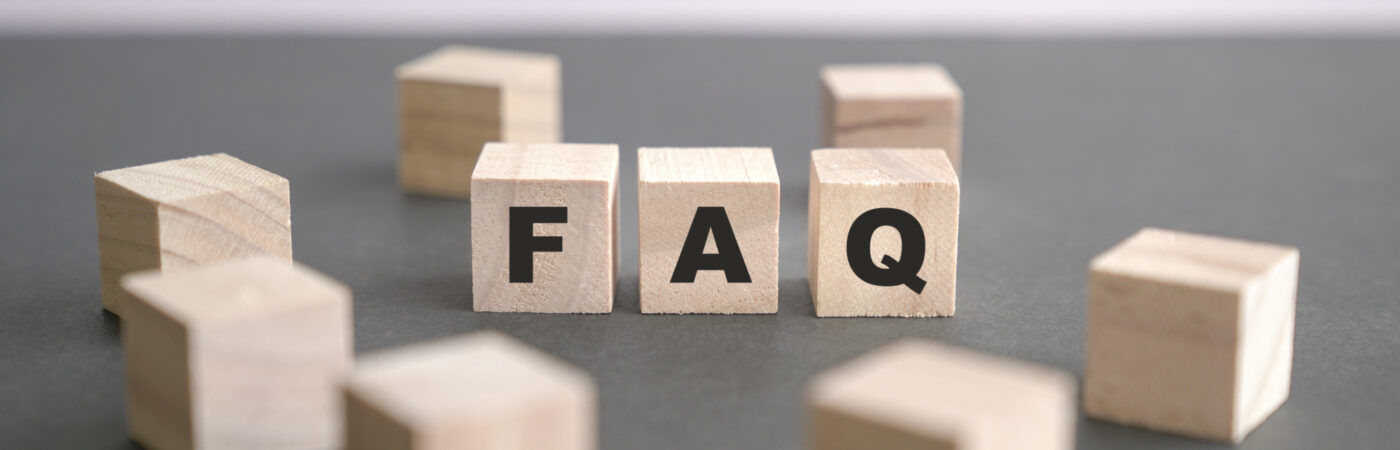
Frequently Asked Questions
James Knights on News · Mar 17, 2023
The DeltaV-Seal is revolutionising static sealing, one gasket at a time. The gasket provides the tightness and durability of a metal-to-metal seal with the ease of application of a spiral wound, semi-metallic, or Kammprofile gasket. Want to know more, we've provided answers to our most frequently asked questions below:
1. Does the DeltaV-Seal damage or scratch flange surfaces?
No. Correct installation is critical to the performance of the DeltaV-Seal. You can download our installation instructions. You can also read our report on the impact of the DeltaV-Seal on flange surfaces.
2. Is the DeltaV-Seal fire safe?
Yes. The DeltaV-Seal has been independently tested by AMTEC, Germany in accordance with API 6FB. The DeltaV-Seal had a leakage rate 1% of the maximum requirement to pass the API 6FB fire safe test. View our API 6FB certification.
3. What is the leakage rate of the DeltaV-Seal?
The leakage rate of any seal varies depending on many variables. All DeltaV-Seal flange gaskets within our standard product library referenced in our installation instructions have a leakage rate below 0.0000001 mg/m/s when installed correctly. We also have the cabability to complete EN1591-1 calculations utilzing TUV certified software to calculate the leakage rate on custom seals.
4. Can you complete calculations in accordance with EN1591-1?
Yes. Please contact us, we'd be delighted to assist. We have a very skilled and tallented engineering team who would enjoy working on your challenge.
5. Have you tested the DeltaV-Seal according to TA Luft / VDI-2440?
Yes. The DeltaV-Seal has been tightness tested at Amtec in Germany, the VDI-2440-test, showing that the DeltaV-Seal is even tighter than the classification ‘Gas Tight’.
Result: 1.01 x 10-08 mbar l/s
View our TA Luft Certification.
6. Is there a summary of the testing completed?
Yes. We believe our gasket is one of the most tested and proven gaskets in the industry. You can download a summary of the testing the DeltaV-Seal gasket has completed here.
7. What are your temperature limits?
We've proven the DeltaV-Seal gasket to be tight and reliable between -196 °C / -321 °F and +880 °C / +1616 °F. Click the links below to view the testing at cryogenic and +880 °C / 1616 °F below.
8. Have you completed testing in accordance with EN13555?
Yes. For all gasket materials within our standard product library we've completed EN13555 testing. Further to the requirements of EN13555 we've also tested our gaskets at elevated temperatures. You can view the EN13555 testing for the S235 carbon steel, 316L stainless steel, and 800HT Incoloy gaskets below:
9. What torque value do I require?
The bolt torque values for all gaskets within our standard product library can be found within our installation instructions. For special seals beyond our standard product library contact us, we'd be happy to help with your sealing challenge.
10. Do I need to lubricate the bolts?
Yes, it is critical the flange bolts are lubricated correctly. Our standard installation instructions consider Molykote® G-Rapid Plus, should you wish to use another lubricant please contact us.
11. Does the DeltaV-Seal require any ongoing maintenance?
No. The DeltaV-Seal is a static, metal-to-metal seal. If the DeltaV-Seal is installed correctly there is no requirement to retighten flange bolts throughtout the lifetime of the seal. Given the all-metal construction of the DeltaV-Seal it is much more resistant to pressure-pulse, vibration, and chemical degradation.
12. Does the DeltaV-Seal have any certifying agency Type Approval?
Yes. To our knowledge the DeltaV-Seal gasket was the first and only metallic gasket which has DNV GL type approval. You can view our DNV GL Type Approval Certificate.
13. Does your gasket contain graphite or PTFE?
No. The DeltaV-Seal is a fully metallic one piece seal with no other materials. The DeltaV-Seal is PFAS free and easy to recycle due to its single material, metallic construction.
14. Has the DeltaV-Seal been tested on damaged flange surfaces?
Yes. We recommend all installations follow the most recent guidance of ASME PCC1. Testing has shown the DeltaV-Seal will seal scratches up to 0.2 mm deep, which is beyond the acceptance criteria of ASME PCC1.
15. What is the diameter range of gaskets Pipeotech supply?
Our standard product library covers a range from 1/2" / DN10 up to 24" / DN600. Should you require a size outside our standard product library please contact us.
16. Is the DeltaV-Seal vibration and pressure pulse resistant?
Yes. The DeltaV-Seal has been exposed to 10 million vibration cycles during DNV GL type approval tests, simultaneously being exposed to pressure pulsation tests, 500 000 pressure pulse sequences, from 0 to 150% of the gaskets pressure class range. The 2", 6" and 12" #300 DeltaV-Seal sizes all underwent this test.
17. What are the M & Y values for the DeltaV-Seal?
Due to the arcitecture and sealing area of the DeltaV-Seal, M&Y values are not functional for modern flange design. Pipeotech completes all calculations according to EN1591-1, which enables the complete bolted flange joint integrity to be calculated. All torque values within our installation instructions are based on EN1591-1, with a leakage rate of 0.0000001 mg/m/s considered. For further assistance calculating torque values using M&Y values please do not hesitate to contact us.
18. Can the DeltaV-Seal be re-used?
No. Standard maintenance practice for all bolted flange gaskets, is that when the flange joint is broken all gaskets are to be replaced with a new gasket.
19. How much does the DeltaV-Seal cost?
All operators who have included the DeltaV-Seal within their best practice have realised significant maintenance and operatational savings compared to traditional gaskets.
20. Is any special qualification or tooling required to install the DeltaV-Seal?
No. All installers need to be to be certified to ASME PCC1 (or equivilent) for the assembly of bolted flange joints. Pipeotech is able to provide all site installation support, either in person or by videolink.
21. What QA/QC procedures are applicable to the manufacture of the DeltaV-Seal?
All DeltaV-Seal products are precission CNC machined. We have a full in-house QA/QC procedure in accordance to strict MPS guidelines. We can provide 3.1 material certificates and 2.1 certificates of conformance for all products manufactured.
22. Do you have a user references and case studies?
Yes. The DeltaV-Seal is being used over an extensive range of industries due to its best-in-class performance. View our case studies.
23. Can the DeltaV-Seal be cleaned and packed to meet specific clean service requirements?
Yes. Due to the one-piece architecture without the inclusion of any filler material cleaing the DeltaV-Seal is simple. We have significant previous experience cleaning and packing gaskets for peroxide service within our facility. Our gasket is also durable and easy to clean on site.
24. How does the DeltaV-Seal mitigate the risk of galvanic corrosion?
Being manufactured from a compatible material to the flange face, the DeltaV-Seal helps to mitigate any potential for galvanic corrosion ensuring a long, leak-free service life for the bolted flange joint. You can learn more about galvanic corrosion and the DeltaV-Seal here.
25. How can I use the DeltaV-Seal to reduce ATEX Zones?
The combination of all the extensive testing completed by Pipeotech (including EN13555, API 6FB, TA Luft VDI 2440, vibration, and pressure) enables a third party certified Professional Engineer to confirm the tightnes and durability of the bolted flange joint and calculate a reduced ATEX zone. We've reduced the ATEX zones in serveral facilities, you can find the links to some of the projects case studies below:
ATEX Zoning reduction & Equipotential bonding
26. Can I meet my net-zero commitment utilizing the DeltaV-Seal?
Yes. The DeltaV-Seal provides an effectively net-zero-emission bolted flange joint, when installed correctly. The performance will meet all known forthcoming legislation applicable to fugitive emissions control and clean air standards, both local and international. You can learn more here.
27. What support can you provide when designing high temperature flanges?
Pipeotech have assisted many companies in designing bolted flange joints for extreme temperatures (up to aproximately 880 °C / 1616 °F), including in Hydrogen service. You can read a report on how we design high temperature flange joints here.
More from News
DNV Type Approval Certificate Renewed
James Knights on News · Oct 22, 2024
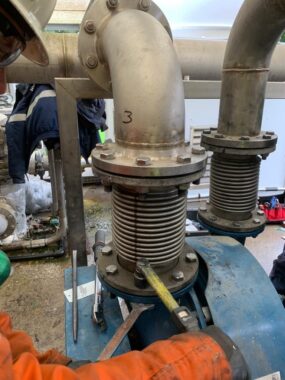
We're pleased to announce the renewal of our DNV Type Approval, valid until 2029. The DNV GL Type Approval (Certificate TAP000003B) celebrates the testing and dedication to achieving the tightest…
COMSOL Multiphysics FEA Modelling of Gasketed Bolted Flange Joints
James Knights on News · Jul 08, 2024
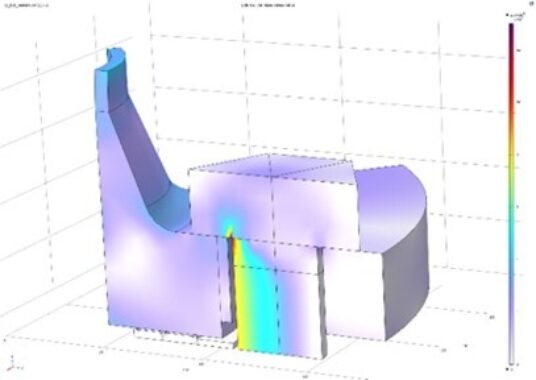
Imagine a future where in extreme environments it is possible to model and simulate a gaskets performance and know the lifetime of a bolted flange joint, sealed with a DeltaV-Seal. Pipeotech's…
Pipeotech launch new 304L stainless steel DeltaV-Seal for nitric acid service
James Knights on News · Jun 21, 2023
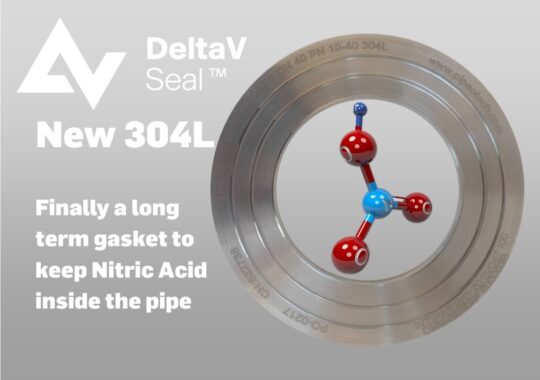
Working with the chemical industries it is clear Nitric Acid is a particularly challenging chemical to keep within bolted flange joints. Current industry practice on bolted flange joints containing…
Proposed European PFAS ban officially submitted – it’s potential impact on PTFE gaskets.
James Knights on News · Mar 17, 2023
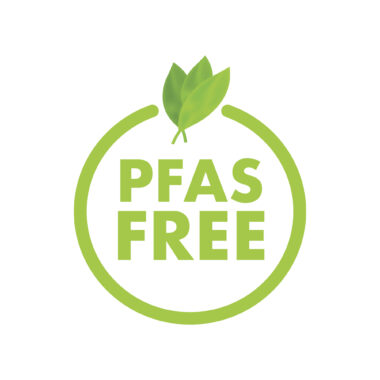
On the 13 January 2023, The Netherlands, Germany, Denmark, Sweden and Norway took the first formal step towards a European ban on polyfluoroalkyl substances (PFAS) by jointly submitting a restriction…
We're growing - and moving to a bigger office space!
James Knights on News · Mar 06, 2023

We are excited to announce that Pipeotech’s Oslo team is moving to a new location within Oslo. The big reason? We are growing in both the number of clients and number of applications where a…
DeltaV-Seal Gaskets for peroxide service featured in Fluid Handling Pro
James Knights on News · Dec 21, 2022
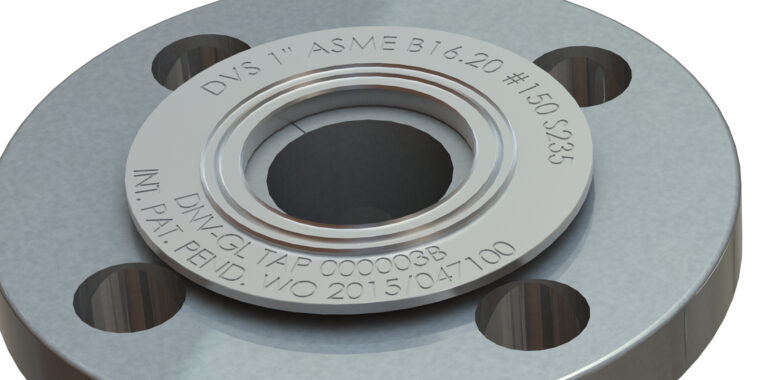
Pipeotech's project with a global manufacturer of peroxide has been featured within Fluid Handling Pro. The article details the design considerations for a gasket utilized in an extremely pure…
Pipeotech Q3 Newsletter
James Knights on News · Oct 20, 2022
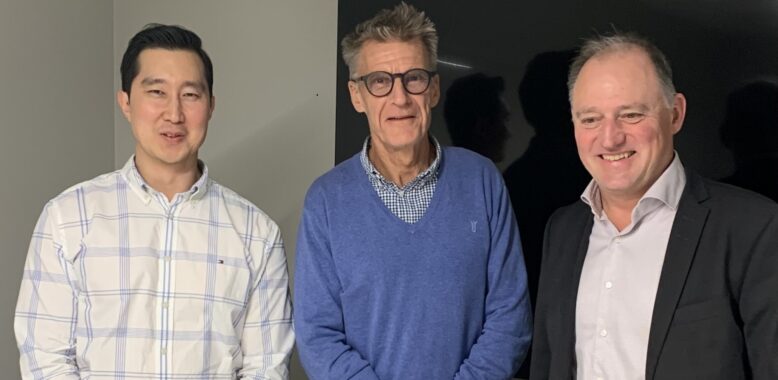
Another quarter is in the books here at Pipeotech. Q3 brought many opportunities for the company. Engineers and executives met with clients across the globe and attended various events to share the…
Pipeotech, featured in Fluid Handing Pro

Jo Shailes on News · Nov 15, 2021
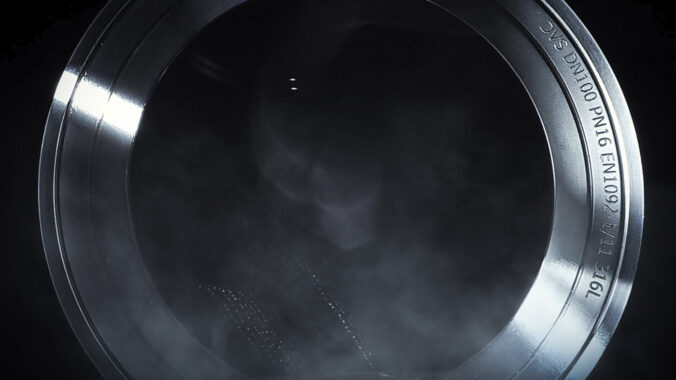
Vibration Analysis Part of the DNV Type Approval for the Pipeotech DeltaV-Seal The weakest link in industrial piping systems is the gasket. Conventional semi-metallic gasket technologies are not able…
Pipeotech, featured in Sealing Technology & World Pumps

Jo Shailes on News · Oct 27, 2021
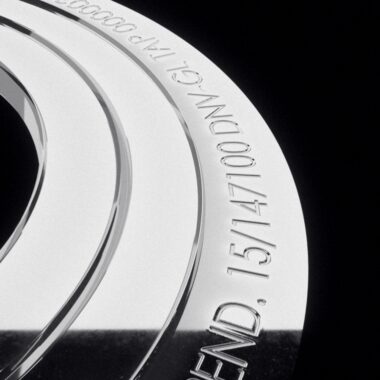
Following extensive leakage testing, carried out under cryogenic conditions in a laboratory programme, Pipeotech has extended coverage all the way down to applications running at a temperature of…
Valve World features DeltaV-Seal™
Geir Otto Amundsen on News · Sep 15, 2021
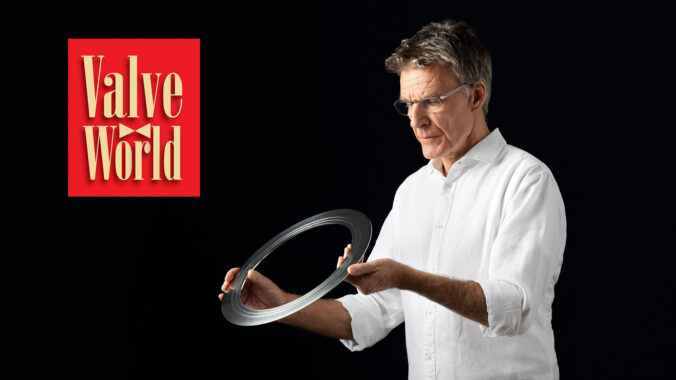
In July 2021, one of the sealing industry's most widely circulated publications, Valve World, featured Pipeotech CTO Jan Oredsson inspecting a DeltaV-Seal gasket on its front cover, hailing Pipeotech…
Andrew Patrick takes over as Pipeotech interim CEO
Geir Otto Amundsen on News · Jun 23, 2021
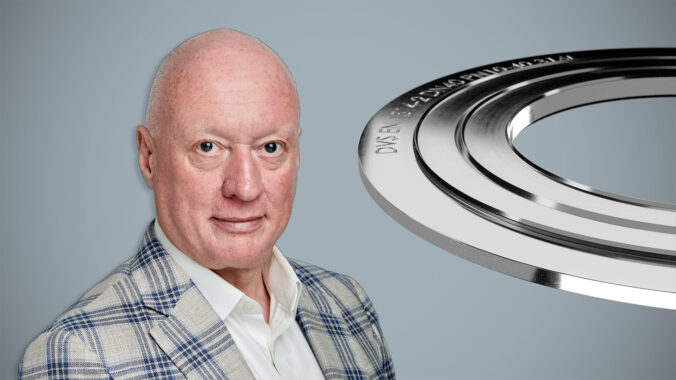
Pipeotech has appointed Andrew Patrick as the company’s interim chief executive following the resignation of outgoing CEO Henrik Sollie. Patrick steps into the interim role from his current position…
Cryogenic milestone for DeltaV-Seal™
Geir Otto Amundsen on News · Mar 31, 2021
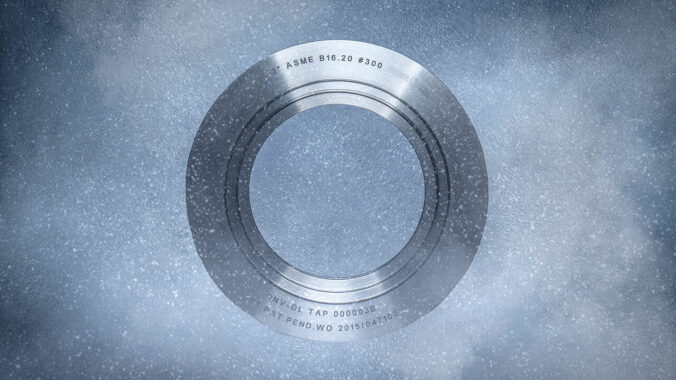
Pipeotech gasket, DeltaV-Seal™ is engineered for long term use, all the way down to applications running at -196°C, based on stellar results of cryogenic leakage tests at a pre-eminent European…
DeltaV-Seal™ - The end to fugitive emissions?
Geir Otto Amundsen on News · Mar 16, 2021
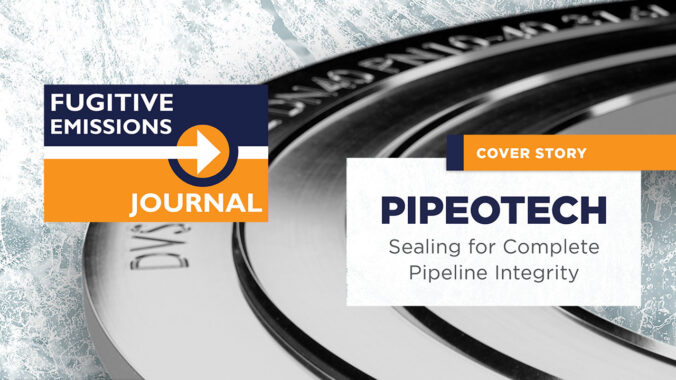
At Pipeotech we believe that the concept of 'acceptable leakage' is unacceptable and that flange-born fugitive emissions are an avoidable threat. As part of our mission to spread this message it was…
Corrosion and integrity specialist Jan Oredsson joins Pipeotech
Geir Otto Amundsen on News · Dec 02, 2020
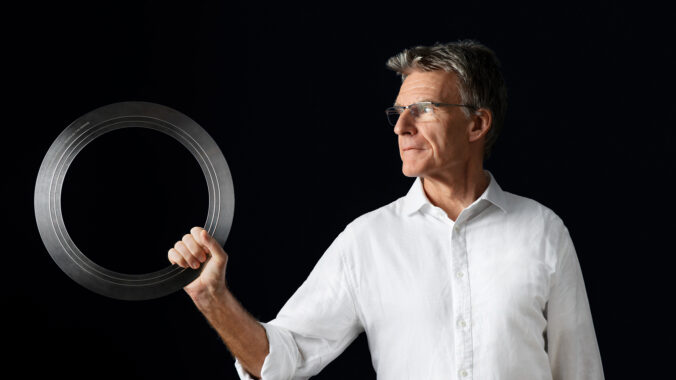
Pipeotech has sealed the deal on an exciting new addition to its team by bringing in internationally recognized pipeline integrity and corrosion expert Jan Oredsson.Oredsson has extensive experience…
Pipeotech recruits Andrew J. Patrick as new Head of Business Development
Geir Otto Amundsen on News · Oct 05, 2020
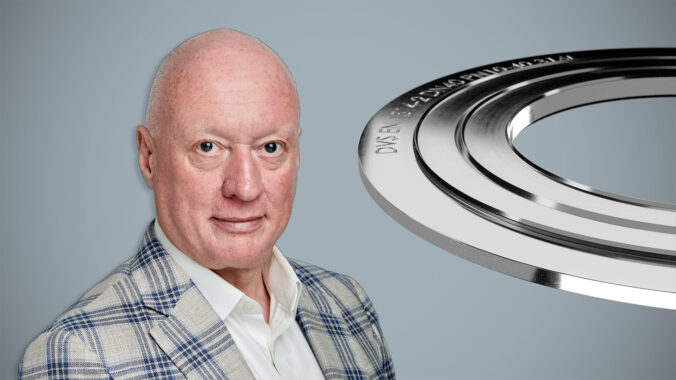
Pipeotech is looking to “supercharge” its global growth with the recruitment of Andrew Patrick to the new role of Head of Business Development. Patrick, previously EVP Global Sales at Clock Spring…
Pipeotech joins the European Sealing Association
Geir Otto Amundsen on News · Jun 28, 2020
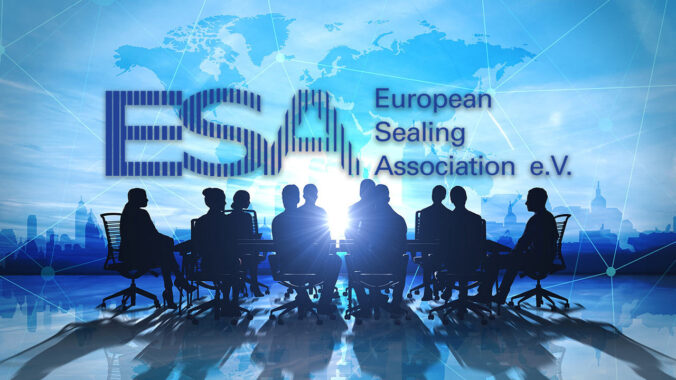
Pipeotech is pleased to announce that it has become a member of the European Sealing Association.Established in 1992 as a non-profit making trade association, The European Sealing Association…
To boldly go... Pipeotech joins the Innovation Norway, Explorer
Geir Otto Amundsen on News · Apr 22, 2020
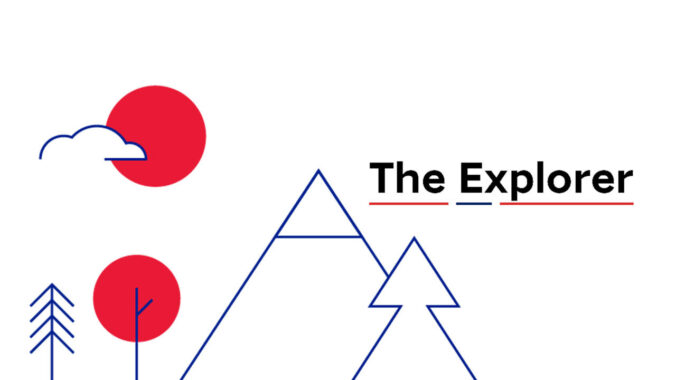
We’re pleased to announce that at the beginning of 2020, Pipeotech joined the ranks of one of Norwegian Industry’s most exclusive clubs, The Explorer. Opened by Norwegian Prime Minister Erna Solberg…
From subsea to life on land - gasket technology follows Darwinism
Geir Otto Amundsen on News · Aug 28, 2019
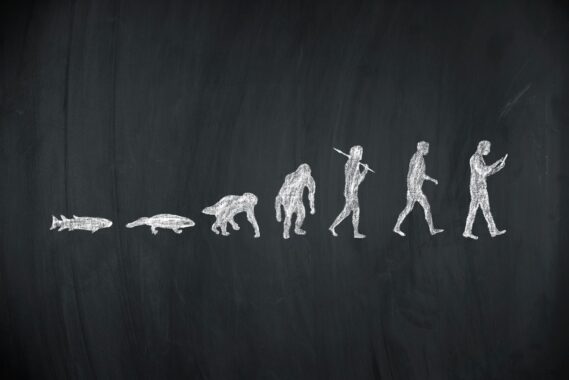
As featured by Yahoo Finance news via Cision PRNewswireMetal-to-metal sealing technology is a technique that had previously been reserved for subsea oil and gas applications where meeting the most…
The seal of integrity (a feature article written by Industry Networker Magazine)
Geir Otto Amundsen on News · Jul 01, 2019
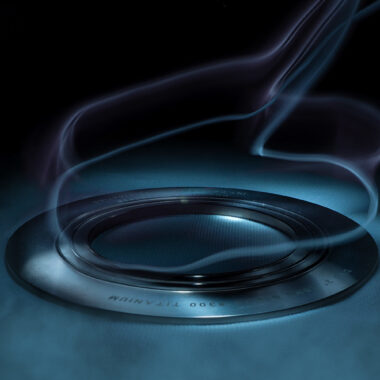
In a recent article published by Industry Networker Magazine, Pipeotech and theDeltaV-Seal™ are recognized for significant technological enhancements towards safety, efficiency, cost reduction, and…