
In conversation with: Odd Skagestad, GE Healthcare Lindesnes
Geir Otto Amundsen on Case Studies · Jun 02, 2021
We recently spent some time talking with technical engineer Odd Skagestad from GE Healthcare Lindesnes about how DeltaV-Seal™ technology has impacted operations at a world-leading pharmaceutical manufacturing facility.
What is your role and responsibility at the plant? How long have you worked there?
I am a departmental engineer in the technical engineering department with equipment responsibility for pipes, valves, gaskets and tanks. In addition, I am responsible for pipes and mechanical disciplines in a number of projects. I’ve been employed at Lindesnes for almost 20 years.
Tell us a bit about the Lindesnes factory - what you are making there now?
GE Healthcare AS, Lindesnes factories, was established in 1974 under the name Nygaard og co. Since then, the site at Lindesnes has become part of global GE Healthcare brand and evolved into a state-of-the-art pharmaceutical process factory that produces X-ray contrast agent. In total, GE healthcare has around 40% of the world market for X-ray contrast agents with around 240,000 patients receiving injections of contrast medium originating from the Lindesnes Factory every single day. We currently have over 400 employees who come primarily from Lindesnes and the surrounding municipalities.
What applications and processes are typically found at the Lindesnes factory?
From a process piping point of view, the facility deals with a wide range of applications including everything from water to solvents, bases, acids and gases. The product itself goes through several process stages, each with very different physical properties that we must take into account when choosing material qualities and gasket types.

– Throughout the facility are approx. 230 km of pipework installed with around 40,000 valves, 2,000 pumps and 700 heat exchangers in total.
...and gaskets?
Of the gaskets at the plant, we use everything from fiber, rubber and graphite gaskets as well as some PTFE and Viton. We are very satisfied and have very little leakage due to the careful selection of gasket types based on the media and process conditions in each pipe run. The biggest factor when selecting a new gasket is quality, secondly price. We have very good experiences with the gaskets we have chosen to use on our systems so far.
What processes are you currently using DeltaV-Seal?
We have now approved DeltaV-Seal on steam, lye, nitrogen and methane pipe runs. We have also installed them on a part of the cooling water system with pipes to and from a buried cooling water tank that we previously had leakage problems on. This has been a success and we have now not detected any leaks where we have used the DeltaV-Seal gaskets.
What led you to installing DeltaV-Seal on a methane system?
At GE Healthcare Lindesnes there is a strong focus on our corporate environmental responsibility. As part of our program of environmental impact reduction measures, we have established a separate process unit dedicated to reducing emissions of TOC (Total Organic Carbon). This is conducted in accordance with the IED (Industrial Emissions Directive EU) limit values set by BAT (Best Available Technology) for different industrial processes.
One of the purification steps that reduce our carbon footprint is the biological decomposition of organic compounds. This is achieved by first using anaerobic purification on an EGSB reactor (Expanded Granular Sludge Bed), where methane is formed for combustion in boiler houses that produce steam. To prevent any leakage including harmful fugitive methane emissions we decided to use the DeltaV-Seal gaskets due to the gas-tight leakage properties and extended service life.
What is your first impressions of our seal? Would you recommend it?
When we were first approached by Pipeotech in 2015 as a potential pilot customer we decided to conduct some in-house testing to verify some of the product claims. Due to our experience with other gaskets dissolving or changing physical properties over time a program to assess the durability and corrosion resistance of the gasket was appropriate. The result was that after prolonged exposure to corrosive saline solutions internally and externally the DeltaV-Seal displayed no signs of any corrosion. Our first impression, therefore, was that it was a very well-developed type of gasket and immediately became the solution to some of our sealing challenges.
The impressive technology forms an extremely tight and static connection with the flange making them stable over time. We really noticed this on steam systems. Before we were using graphite spiral wound gaskets which proved extremely challenging to disassemble during maintenance, often requiring machining of the flange surface. Here, the simplicity of the one-piece metal construction of DeltaV-Seal comes into its own.


– The result was that after prolonged exposure to corrosive saline solutions internally and externally the DeltaV-Seal displayed no signs of any corrosion.
And whats it been like dealing with Pipeotech?
Pipeotech delivers good products and is a customer solution-oriented company. We have been in dialogue with them when we were first introduced to the technology to optimize the design for our use. On initial testing on some of our non-standard systems, it turned out that one of the three grooves in the gasket surface did not hit the gasket surface on the flange collar. Pipeotech solved this by changing the position of the grooves, creating a custom design for our needs so that the sealing rings would correctly seal against the flange collar. We really appreciate this kind of service and see it as a big advantage for Pipeotech.
More from Case Studies
DeltaV-Seal increases available up-time on Ammonium Nitrate flanges
James Knights on Case Studies · Sep 16, 2024
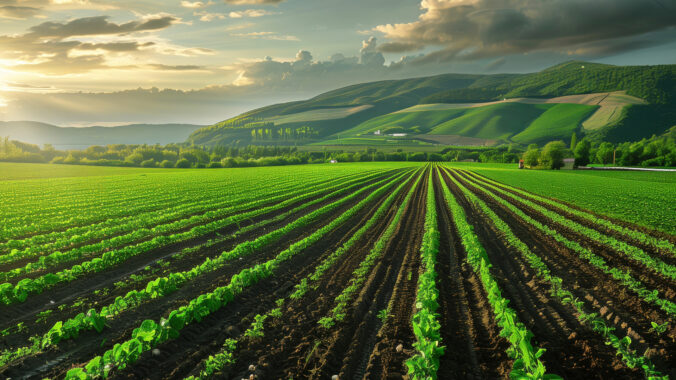
Legacy semi-metallic gaskets leak, this is particularly visible on Ammonium Nitrate flanges. The DeltaV-Seal provides a significantly tighter seal than legacy gaskets, enabling fertilizer…
DeltaV-Seal - Preventing emissions of NOX gas during fertilizer manufacture
James Knights on Case Studies · Sep 16, 2024
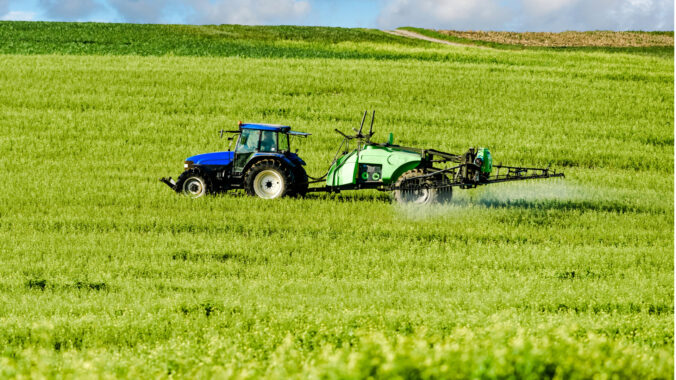
NOX is considered an indirect greenhouse gas, with strict PPM values for the amount of emissions a chemical plant can release. The DeltaV-Seal with its tight and durable seal prevents emissions of…
DeltaV-Seal - Reducing fugitive emissions in the Permian Basin
James Knights on Case Studies · Jul 22, 2024
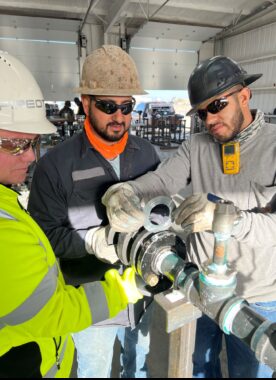
The United States Clean Air Act (CAA) is the comprehensive federal law regulating emissions from stationary and mobile sources. Among other things the CAA authorises the United States Environment…
Best Available Technology to reduce ATEX zones, increase reliability, and improve safety within a refinery
James Knights on Case Studies · Jul 21, 2023
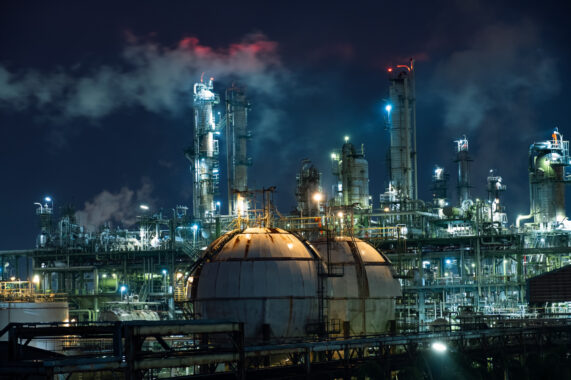
Europe’s most advanced refinery wanted to further pioneer by only utilizing Best Available Technology to ensure a safe and reliable operation with minimal impact on the environment, enhanced…
FPSO & Marine - DeltaV-Seals ensure the safe and reliable operation of inert gas systems
James Knights on Case Studies · Mar 21, 2023
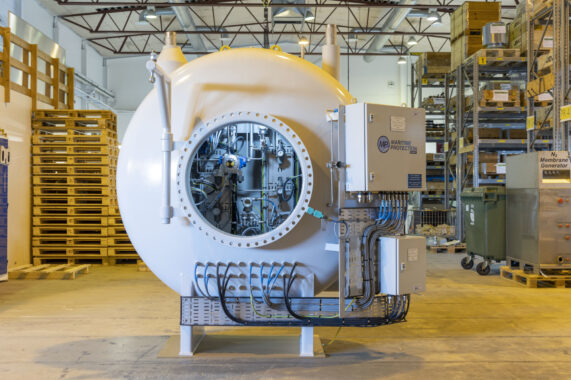
A market-leading expert for the maritime industry manufactures a range of inert gas generators to suit their client's needs. Vessels carrying cargo-producing hydrocarbon vapors require inert gas…
Preventing nitrous gas leakage at a Thermowell instrument flange joint
James Knights on Case Studies · Mar 09, 2023
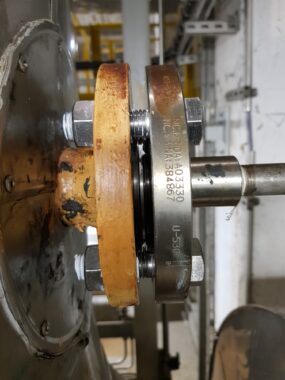
On a Thermowell instrument coupling flange joint a previous semi-metallic gasket required maintenance intervention 7 times in three-and-a-half years. Switching from a semi-metallic gasket to the…
Semi Conductor application for Nitrogen and Oxygen gas purifiers
James Knights on Case Studies · Feb 27, 2023
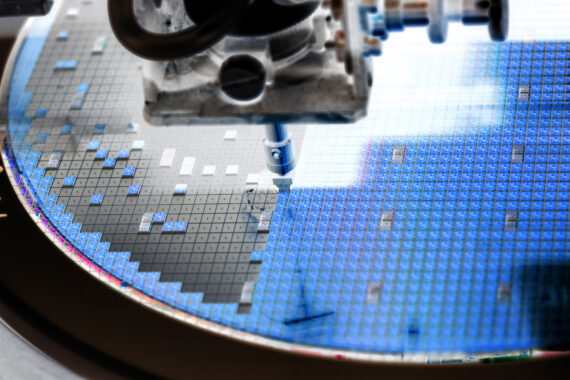
One of the world's leading semiconductor manufacturers in South Korea required a carbon-free, bacteria and virus-tight gasket capable of withstanding temperatures up to 500°C. The DeltaV-Seal™…
ATEX Zoning reduction & Equipotential bonding possible with the DeltaV-Seal
James Knights on Case Studies · Jan 09, 2023
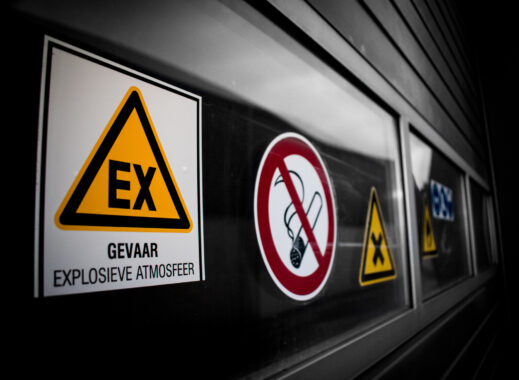
Recycling metallic canisters containing flammable gases to prevent the emission of the gases to the environment and recycle the metallic packing material.
Reducing ATEX zoning within a biogas plant
James Knights on Case Studies · Nov 11, 2022
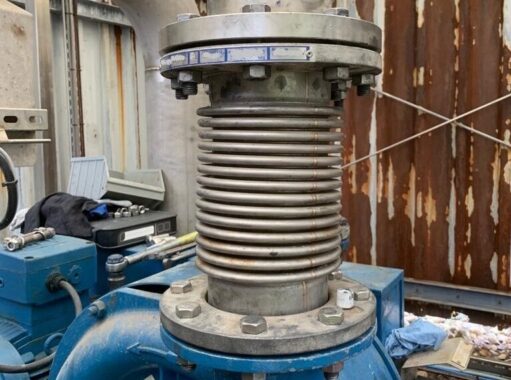
Local regulation of a biogas plant in Western Europe required ATEX zoning. Utilizing several technical standards including EN1127, EN1591, and Pipeotech's extensive library of product testing, it has…
Cleaned gaskets within a peroxide system of a chemical processing plant
James Knights on Case Studies · Oct 11, 2022
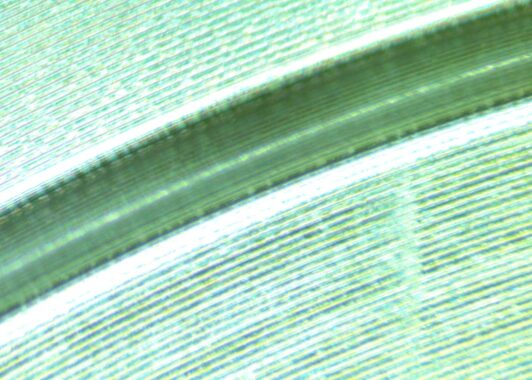
Ensuring product quality and plant safety with a clean, bespoke, tight, and durable seal. The DeltaV-Seal enabled a manufacturer of peroxide to ensure their product was made safely and was free of…
Corporate environmental responsibility ‘done right’ with long-term methane mitigation by design

Jo Shailes on Case Studies · Nov 02, 2021
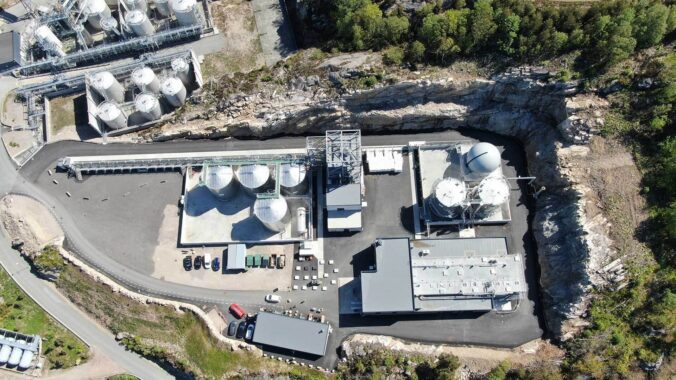
Methane is one of the most potent greenhouse gases and avoiding leakage is a priority when using methane systems. Methane also ignites easily, so there are clear and immediate HSE incentives for…
Gasket ensures a long-lasting seal
James Knights on Case Studies · Nov 02, 2021
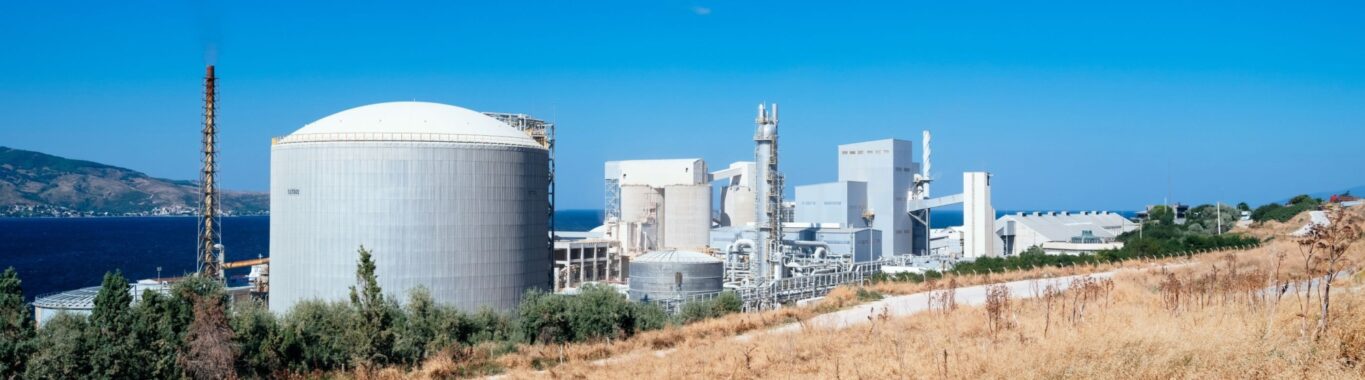
In manufacturing fertilizer, ammonium nitrate is added to the process, and traditional, spiral wound and Gylon gasket technology often deteriorate in these conditions, resulting in leaks. This is…
ATEX zoning unnecessary with DeltaV-Seal™

Jo Shailes on Case Studies · Nov 01, 2021
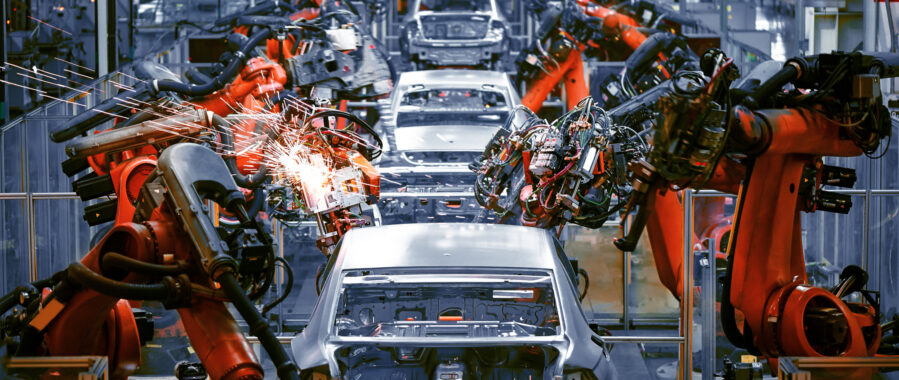
During final assembly in the factory, cars are filled with fuel before being transported to their final destination. To facilitate this, fuel lines run throughout the facility. However, along the…
DeltaV-Seal™ stops flammable leakage, prevent fires

Jo Shailes on Case Studies · Nov 01, 2021
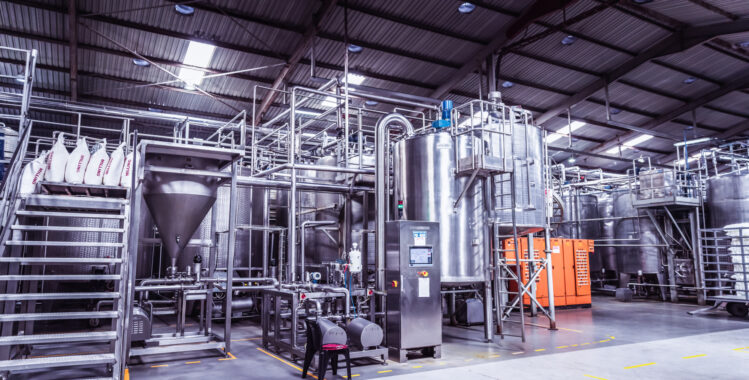
In facilities that use hot oil heat transfer fluid systems, fire hazards are a significant challenge due to the combination of organic combustible liquids, which run at temperatures above their flash…
DeltaV-Seal™ prevent fires, promote safe environment

Jo Shailes on Case Studies · Nov 01, 2021
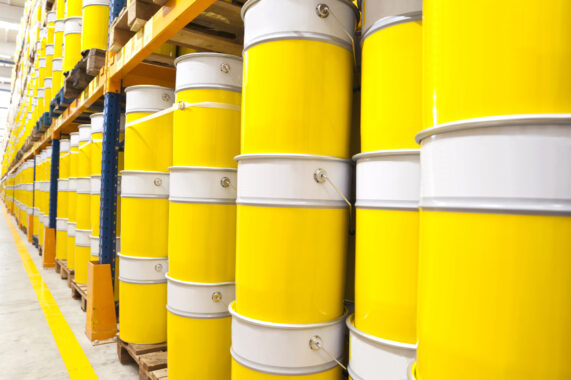
The use of hot oil systems in manufacturing presents challenges when traditional gaskets breakdown and cause leakage. As liquids in the system are kept at a temperature above their flash point, when…
DeltaV-Seal™ prevents leaks and pipe corrosion

Jo Shailes on Case Studies · Nov 01, 2021
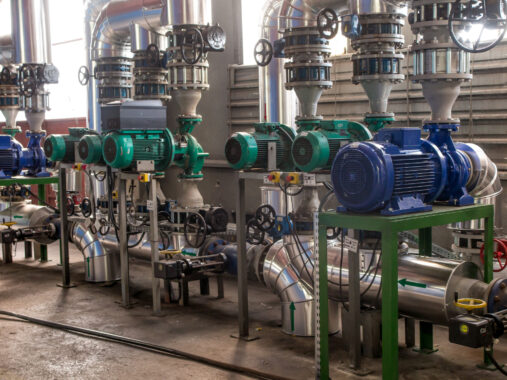
In district heating and cooling, generic spiral wound gaskets frequently cannot cope with the cyclical temperature conditions and often fail, leading to leakages and corrosion of the pipeline. This…
DeltaV-Seal™ performs under extreme marine conditions

Jo Shailes on Case Studies · Nov 01, 2021
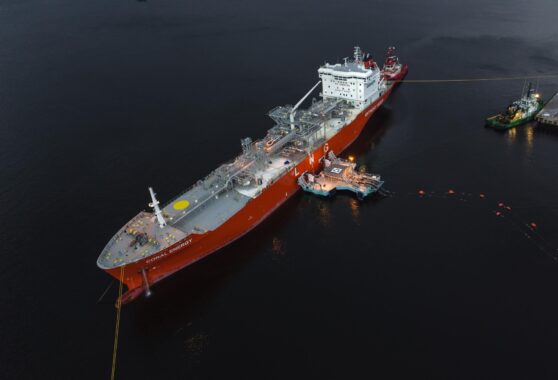
Importing ship-to-shore Liquefied Natural Gas (LNG) requires robust and efficient pipeline seals that are compliant with high environmental standards. The thermal cycling caused by the cryogenic…
DeltaV-Seal™ reduces greenhouse emissions

Jo Shailes on Case Studies · Nov 01, 2021
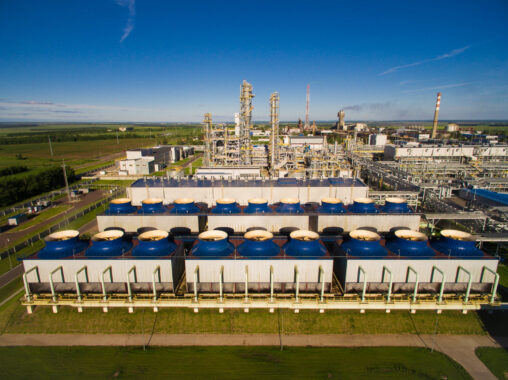
In fertilizer production, high-quality phosphorus fertilizers require nitric acid as a key ingredient, which is usually synthesized via the Ostwald process on-site (oxidizing of ammonia before…
Pipeotech’s reach goes atomic
Geir Otto Amundsen on Case Studies · Jan 05, 2021
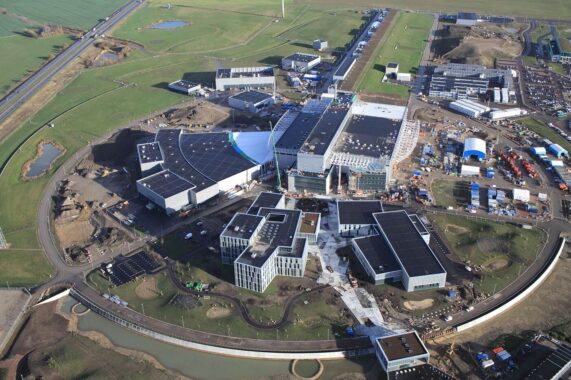
Pipeotech has taken gasket tightness to new microscopic levels by supplying DeltaV-Seal™ to European Spallation Source, the world’s most powerful neutron source, in Lund, Sweden. The new research…
VARD finds the perfect fit

Jo Shailes on Case Studies · Nov 11, 2020
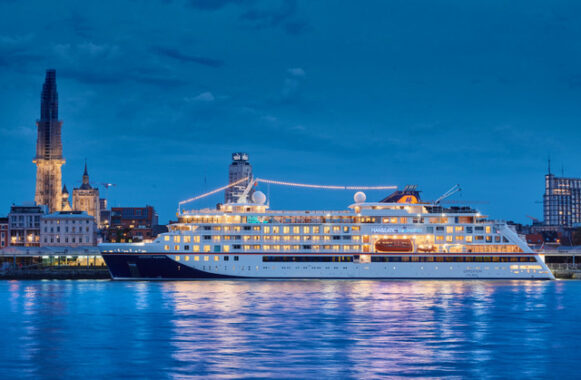
Norwegian-based shipbuilder VARD has been installing Pipeotech’s DeltaV-Seal™ in its vessels since 2016 and the cost-saving benefits have been very clear to Johny Morland, Principal Engineer, QA and…
Corrosive influence - The dangers of galvanic corrosion for pipelines
Geir Otto Amundsen on Case Studies · Apr 22, 2020
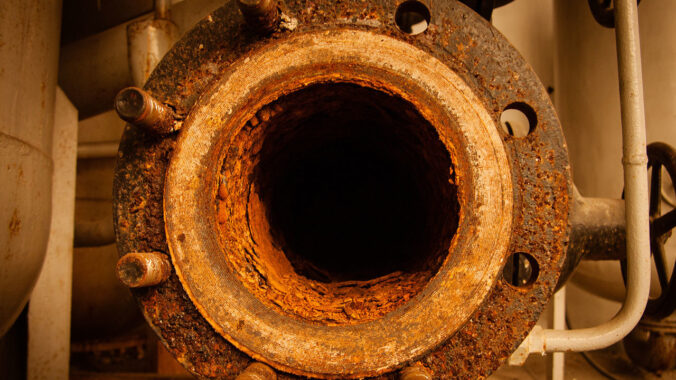
Prevention is always better than a cure. Avoiding issues in the first place, rather than attending to them once they’ve occurred, is plain common sense. So why do so many industrial facilities…
Pipeline safety – How gasket choices can mitigate health and safety risks
Geir Otto Amundsen on Case Studies · Jan 31, 2020
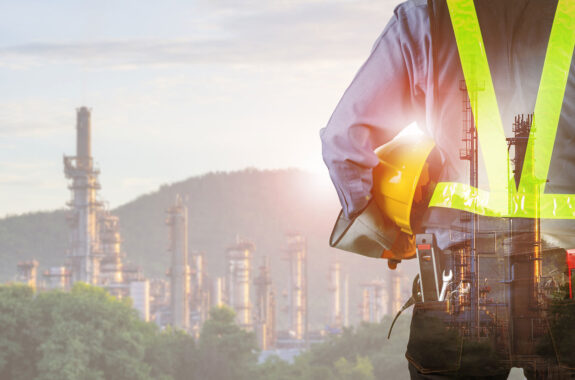
Nothing is as important as health and safety when it comes to industrial facilities. However, a critical component in piping systems is often overlooked, viewed as a consumable rather than a key to…
Stopping expensive leakages at historic brewing facility
Geir Otto Amundsen on Case Studies · Jan 31, 2020
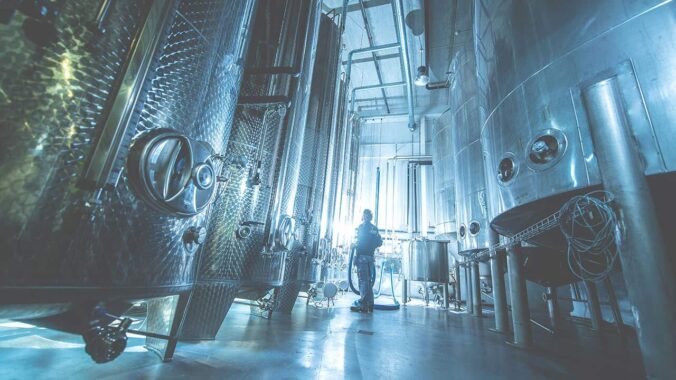
With the title of ‘the oldest brewery in Norway’, the Aass brewery is about as close as it gets to being a Norwegian institution. Situated on the banks of the river in the busy port city of Drammen…
DeltaV-Seal™ replaces kammprofile gaskets at critical distribution facility

Jo Shailes on Case Studies · Jun 12, 2019
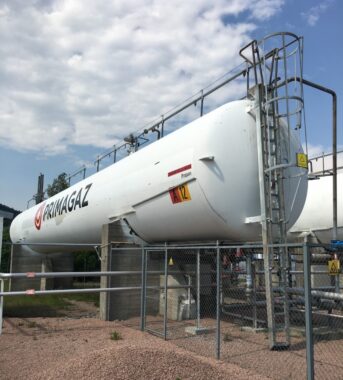
After a long relationship utilizing kammprofile gasket technology, Norwegian LPG distributor PrimaGaz Norge AS has decided to abandon the old kammprofile gasket design in favor of the new DeltaV-Seal…
Flare tip leakage is too hot to handle for the competition
James Knights on Case Studies · May 15, 2019
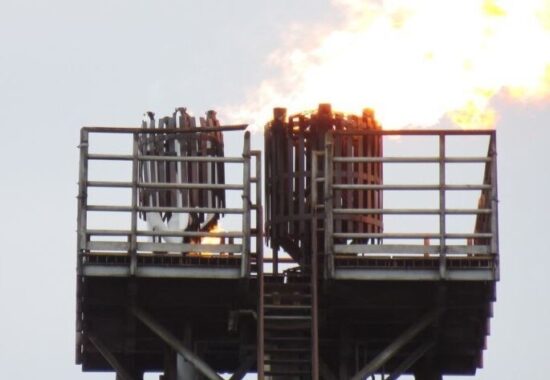
Pipeotech was called upon to provide a solution for Flare Tip flange leak in the North Sea. A North Sea Operator came to Pipeotech with a problem affecting a Flare line on their platform. This was…
Exceeding gas-tight sealing strengths and eliminating ATEX zones
Geir Otto Amundsen on Case Studies · May 08, 2019
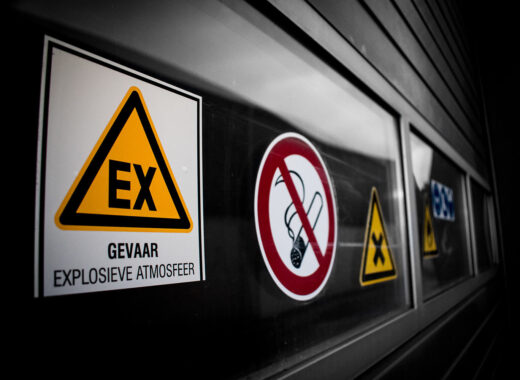
Gaskets seals are generally the consumables often selected at the last moment in a design project and carry few expectations. Although viewed as less significant, this consumable can have the most…
Intergas exclusively use DeltaV-Seal™

Jo Shailes on Case Studies · Mar 26, 2019
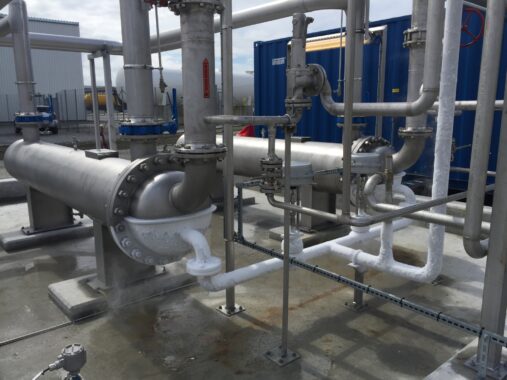
Following a highly successful test period, Intergas AS has announced that the DeltaV-Seal has been named as their exclusive seal of choice for all current and future liquefied natural gas operations.…