
Exceeding gas-tight sealing strengths and eliminating ATEX zones
Geir Otto Amundsen on Case Studies · May 08, 2019
Gaskets seals are generally the consumables often selected at the last moment in a design project and carry few expectations. Although viewed as less significant, this consumable can have the most severe impact on human health, the environment, and a production facility’s revenue. The DeltaV-Seal™ is the first leak-proof and patented sealing technology approved by DNV, delivering revolutionary change by enabling the reduction of operating expenditures associated with the production, maintenance, and product loss.

The avoidable threat
All forms of industrial production of gases or liquids utilize pipes, flanges, and seals. Traditional sealing solutions are an indisputable weak point in any piping system due to their leak-prone nature and life span degradation. Despite the countless safeguards and precautionary measures that are implemented in process piping and production facilities, current sealing solutions still represent significant risks to health, safety, investments, and the environment.
From conception, the primary design purpose of the DeltaV-Seal has been to completely eliminate emissions from flanges in a piping network; in-turn enabling a client to greatly increase operating efficiencies and reduce overall costs. This also enables a significant reduction in environmental contamination that a processing facility or piping system may otherwise have on an environment.
Environmental dangers and sensitive environments identified as ATEX zones can now be addressed with a substantially more cost-effective approach, as the stable sealing strengths of the DeltaV-Seal enables clients to build facilities and piping networks through these zones without the threat of explosion, leakage, or contamination. The DeltaV-Seal is not simply another gasket or consumable associated with production expenditures. It is a game-changing tool and investment, which substantially reduces operating expenditures, increases safety standards, and gives clients greater flexibility in their daily operations by eliminating ATEX zones.

What are ATEX zones?
Hazardous Areas (Potentially Explosive Atmospheres) are defined in terms of zones and safe areas under relevant IEC (for IECEx) and EN (for ATEX) standards depending on the expected frequency and duration of an explosive atmosphere being present.
- Zone 0 / 20: Are zones with constant danger
Permanent presence of explosive gasses or combustive dust. - Zone 1 / 21: Are zones with potential danger
Occasional presence of explosive gasses or combustible dust during normal duty. - Zone 2 / 22: Are zones with minor danger
Presence of explosive gasses or combustible dust is not likely to occur or only for a shorter period of time.
– The DeltaV-Seal is constructed such that it maintains enhanced tightness during its lifetime due to its design, and ensures performance against leakage. By installing the DeltaV-Seal, the user of the equipment can perform a risk assessment to demonstrate the absence of any releases, and eliminate the ATEX zone.
Christoffer Næss, Design & Product Engineer, Pipeotech

Precision engineering
For maximum versatility, durability, safety, and quality consistency the DeltaV-Seal is water cut and then finished via CNC machining for pinnacle precision. Superior quality is further demonstrated, as the gasket is also engineered to withstand both cryogenic and scorching temperatures.
DeltaV-Seal is always manufactured from the same metal alloy as the connecting flanges enabling both seal and flange to expand or contract in unison during temperature fluctuations. The gasket maintains the tightest seating while eliminating the possibility of galvanic corrosion from developing within the connection.

Verified perfection
Tests conducted by DNV and AMTEC GmbH demonstrate sealing strengths that exceed oil and gas industry standards. The DeltaV-Seal has been certified as a Fire and Blowout Safe gasket sealing solution in accordance with API 6FB regulations. Through controlled extreme heat and pressure tests, lasting 30 minutes in length the gasket was exposed to temperatures in excess of 650C and 40 bar of pressure. Test results revealed that the DeltaV-Seal released only 1% of the permitted volume.

DeltaV-Tight
Germany’s 'TA Luft' is a national air quality regulation that sets standards for emissions, ambient exposures and control methods. In a powerful demonstration of DeltaV-Seal’s ability to not just comply, but far exceed regulatory demands, AMTEC GmbH conducted a TA Luft Helium test in accordance with VDI 2440 guidelines. Pipeotech’s revolutionary solution was certified as a 'high-grade sealing system', sealing an incredible 10,000 times tighter than industry requirements.
To be approved by DNV, the DeltaV-Seal had to undergo a unique durability test, not ever been completed by any other gasket. Extensive vibration and pressure pulsation tests were carried out as part of the rigorous test program to document its resistance towards pressure pulses and vibrations over time.
These additional testing revealed the gasket to resist mechanical stress and vibrations greater than 10 million repetitions. These results also enabled it to receive the first DNV certification for gasket sealing technology.
– Unlike Spiral Wound and Kammprofile gaskets, the non-resilient design of the DeltaV-Seal never requires any re-torquing after installation. The elimination of re-torquing enables the seal and flange to offer a longer, maintenance-free, life span.
Jarle Ribler, Chief Technical Officer, Pipeotech
How does it work?
When forces from the mating flanges are applied to the sealing rings, the sharp edges of the rings perfectly adapts to the imperfections of the mating flange surface, creating a perfect gas-tight seal.
The DeltaV-Seal does not degrade or change properties while in operation, eliminating residue from building up, as well as the need for flange cleaning. It effectively lasts as long as the piping network it joins together.
As clients continue to invest in the implementation of the DeltaV-Seal, adjustments are made to the design to accommodate new applications. Regardless of a client's requirements, the DeltaV-Seal continues to prove its value through superior sealing performance, structural integrity, versatility, and ease of operation.
We invite you to contact us with your questions or concerns, all inquiries are welcome!
Contact usMore from Case Studies
DeltaV-Seal increases available up-time on Ammonium Nitrate flanges
James Knights on Case Studies · Sep 16, 2024
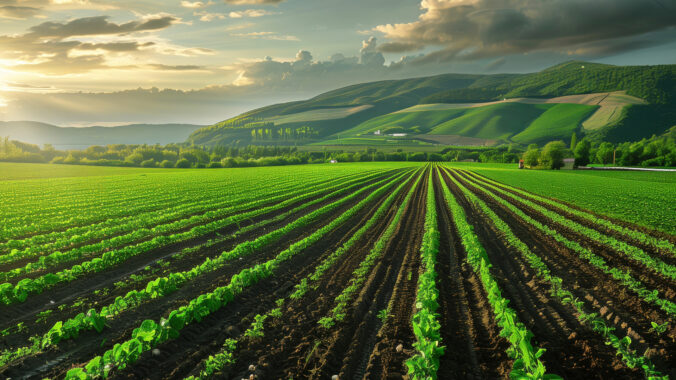
Legacy semi-metallic gaskets leak, this is particularly visible on Ammonium Nitrate flanges. The DeltaV-Seal provides a significantly tighter seal than legacy gaskets, enabling fertilizer…
DeltaV-Seal - Preventing emissions of NOX gas during fertilizer manufacture
James Knights on Case Studies · Sep 16, 2024
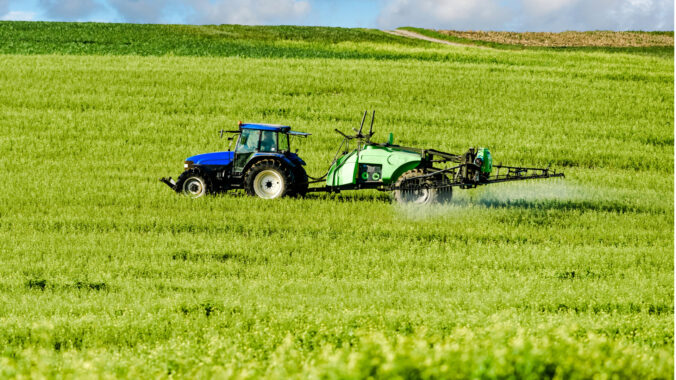
NOX is considered an indirect greenhouse gas, with strict PPM values for the amount of emissions a chemical plant can release. The DeltaV-Seal with its tight and durable seal prevents emissions of…
DeltaV-Seal - Reducing fugitive emissions in the Permian Basin
James Knights on Case Studies · Jul 22, 2024
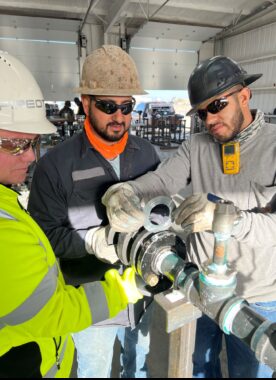
The United States Clean Air Act (CAA) is the comprehensive federal law regulating emissions from stationary and mobile sources. Among other things the CAA authorises the United States Environment…
Best Available Technology to reduce ATEX zones, increase reliability, and improve safety within a refinery
James Knights on Case Studies · Jul 21, 2023
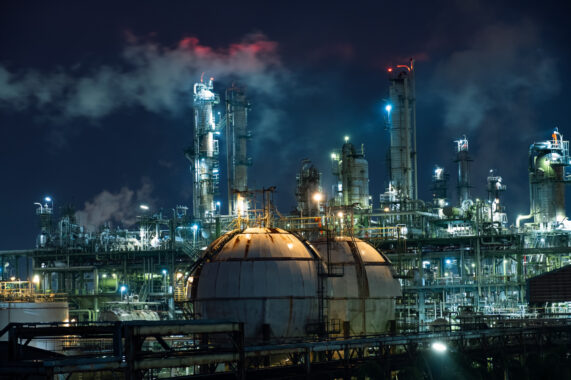
Europe’s most advanced refinery wanted to further pioneer by only utilizing Best Available Technology to ensure a safe and reliable operation with minimal impact on the environment, enhanced…
FPSO & Marine - DeltaV-Seals ensure the safe and reliable operation of inert gas systems
James Knights on Case Studies · Mar 21, 2023
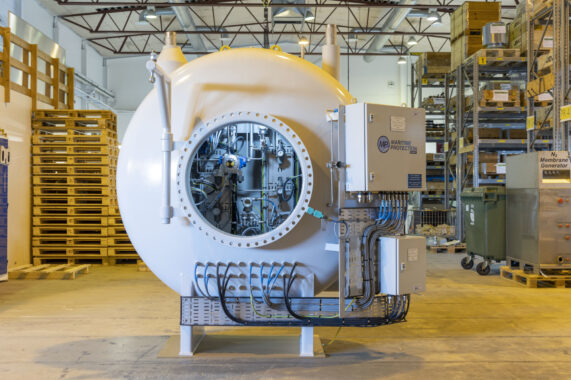
A market-leading expert for the maritime industry manufactures a range of inert gas generators to suit their client's needs. Vessels carrying cargo-producing hydrocarbon vapors require inert gas…
Preventing nitrous gas leakage at a Thermowell instrument flange joint
James Knights on Case Studies · Mar 09, 2023
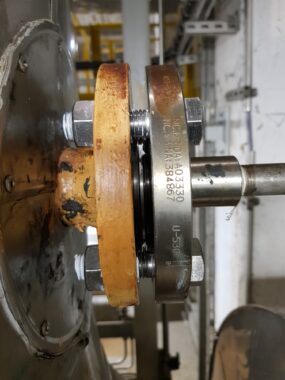
On a Thermowell instrument coupling flange joint a previous semi-metallic gasket required maintenance intervention 7 times in three-and-a-half years. Switching from a semi-metallic gasket to the…
Semi Conductor application for Nitrogen and Oxygen gas purifiers
James Knights on Case Studies · Feb 27, 2023
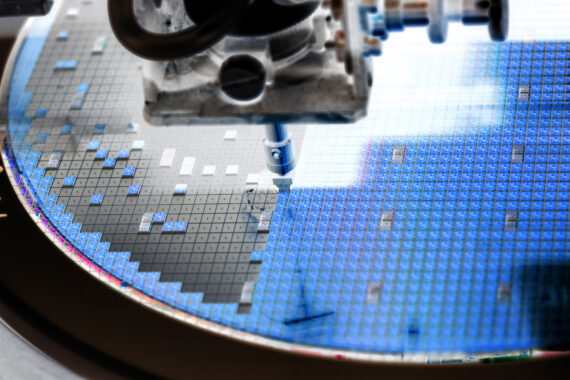
One of the world's leading semiconductor manufacturers in South Korea required a carbon-free, bacteria and virus-tight gasket capable of withstanding temperatures up to 500°C. The DeltaV-Seal™…
ATEX Zoning reduction & Equipotential bonding possible with the DeltaV-Seal
James Knights on Case Studies · Jan 09, 2023
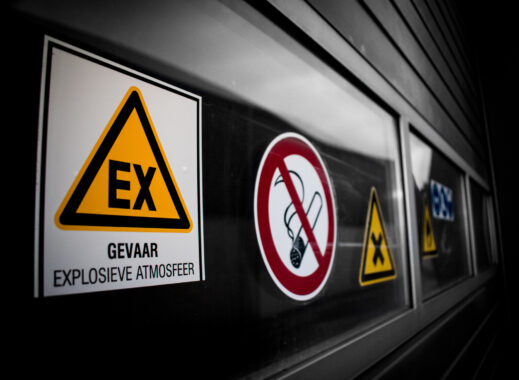
Recycling metallic canisters containing flammable gases to prevent the emission of the gases to the environment and recycle the metallic packing material.
Reducing ATEX zoning within a biogas plant
James Knights on Case Studies · Nov 11, 2022
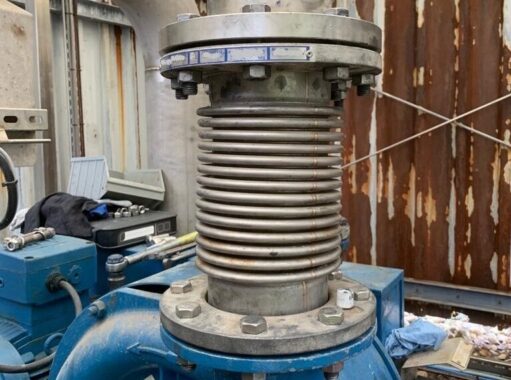
Local regulation of a biogas plant in Western Europe required ATEX zoning. Utilizing several technical standards including EN1127, EN1591, and Pipeotech's extensive library of product testing, it has…
Cleaned gaskets within a peroxide system of a chemical processing plant
James Knights on Case Studies · Oct 11, 2022
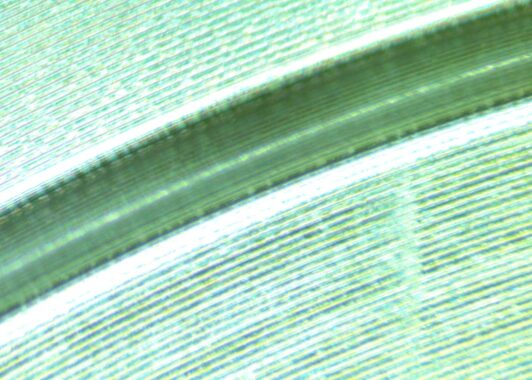
Ensuring product quality and plant safety with a clean, bespoke, tight, and durable seal. The DeltaV-Seal enabled a manufacturer of peroxide to ensure their product was made safely and was free of…
Corporate environmental responsibility ‘done right’ with long-term methane mitigation by design

Jo Shailes on Case Studies · Nov 02, 2021
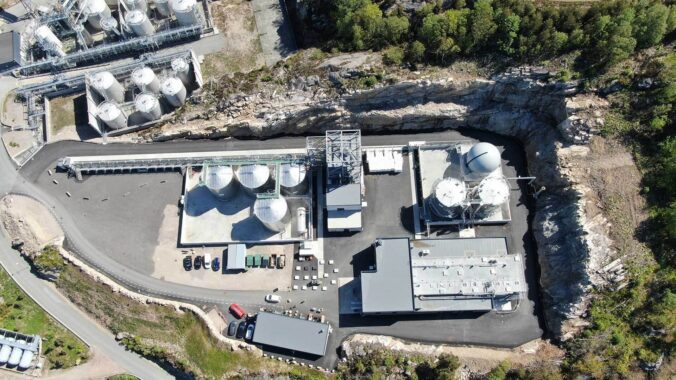
Methane is one of the most potent greenhouse gases and avoiding leakage is a priority when using methane systems. Methane also ignites easily, so there are clear and immediate HSE incentives for…
Gasket ensures a long-lasting seal
James Knights on Case Studies · Nov 02, 2021
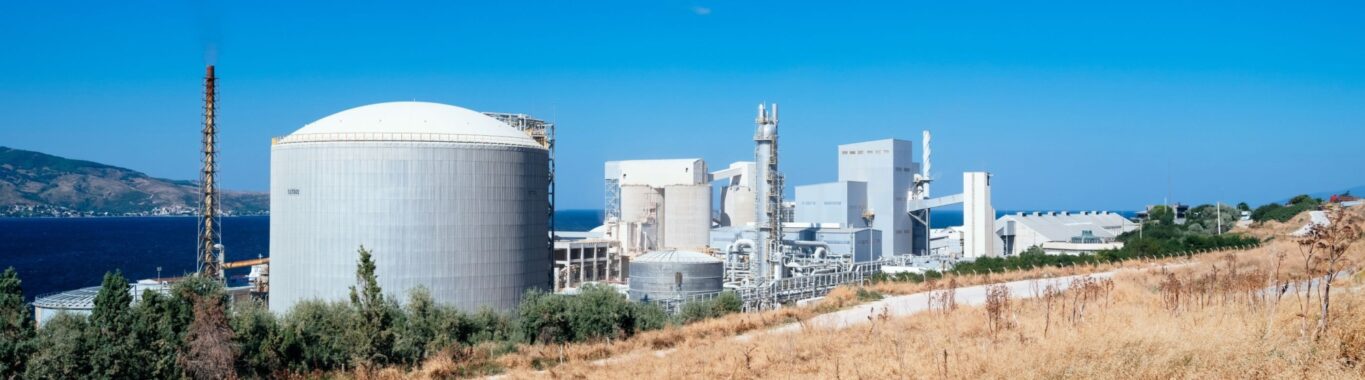
In manufacturing fertilizer, ammonium nitrate is added to the process, and traditional, spiral wound and Gylon gasket technology often deteriorate in these conditions, resulting in leaks. This is…
ATEX zoning unnecessary with DeltaV-Seal™

Jo Shailes on Case Studies · Nov 01, 2021
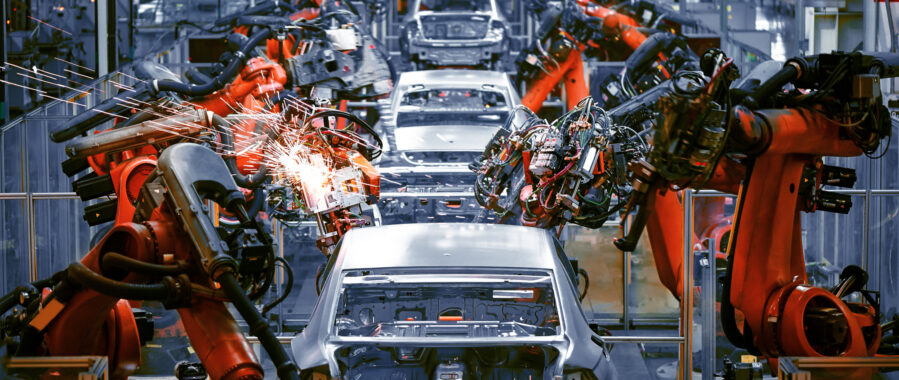
During final assembly in the factory, cars are filled with fuel before being transported to their final destination. To facilitate this, fuel lines run throughout the facility. However, along the…
DeltaV-Seal™ stops flammable leakage, prevent fires

Jo Shailes on Case Studies · Nov 01, 2021
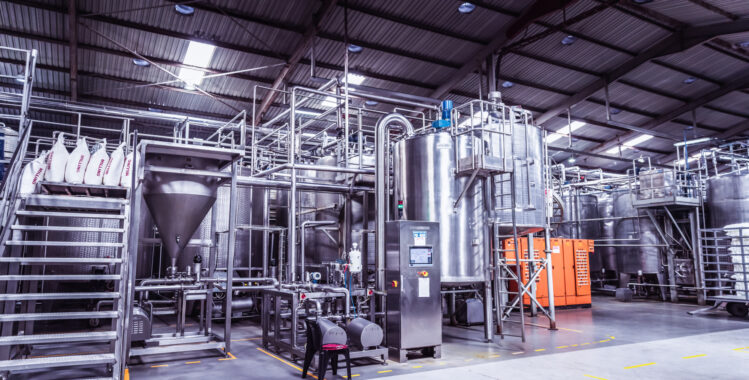
In facilities that use hot oil heat transfer fluid systems, fire hazards are a significant challenge due to the combination of organic combustible liquids, which run at temperatures above their flash…
DeltaV-Seal™ prevent fires, promote safe environment

Jo Shailes on Case Studies · Nov 01, 2021
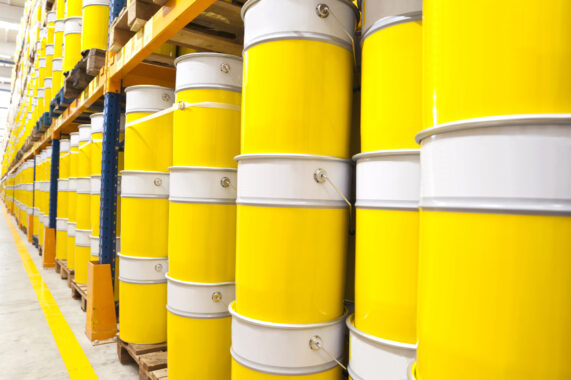
The use of hot oil systems in manufacturing presents challenges when traditional gaskets breakdown and cause leakage. As liquids in the system are kept at a temperature above their flash point, when…
DeltaV-Seal™ prevents leaks and pipe corrosion

Jo Shailes on Case Studies · Nov 01, 2021
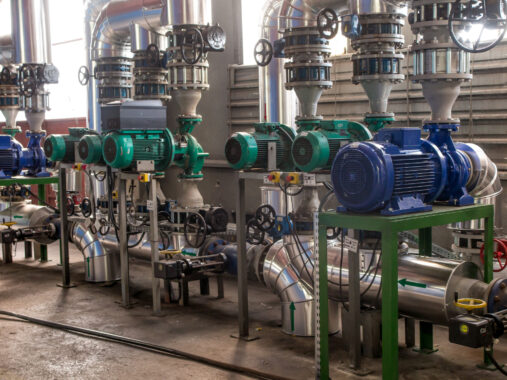
In district heating and cooling, generic spiral wound gaskets frequently cannot cope with the cyclical temperature conditions and often fail, leading to leakages and corrosion of the pipeline. This…
DeltaV-Seal™ performs under extreme marine conditions

Jo Shailes on Case Studies · Nov 01, 2021
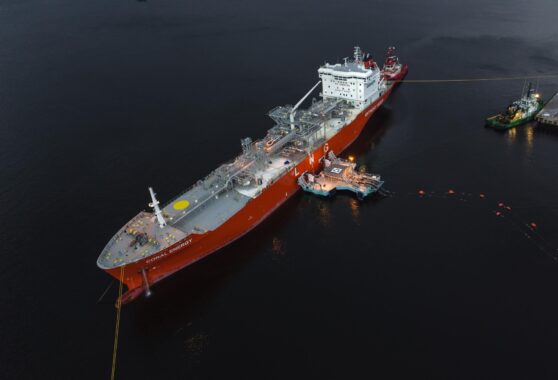
Importing ship-to-shore Liquefied Natural Gas (LNG) requires robust and efficient pipeline seals that are compliant with high environmental standards. The thermal cycling caused by the cryogenic…
DeltaV-Seal™ reduces greenhouse emissions

Jo Shailes on Case Studies · Nov 01, 2021
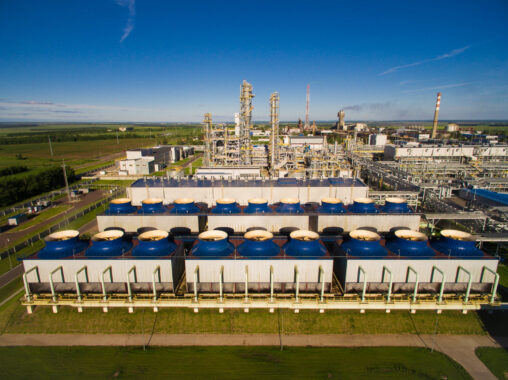
In fertilizer production, high-quality phosphorus fertilizers require nitric acid as a key ingredient, which is usually synthesized via the Ostwald process on-site (oxidizing of ammonia before…
In conversation with: Odd Skagestad, GE Healthcare Lindesnes
Geir Otto Amundsen on Case Studies · Jun 02, 2021
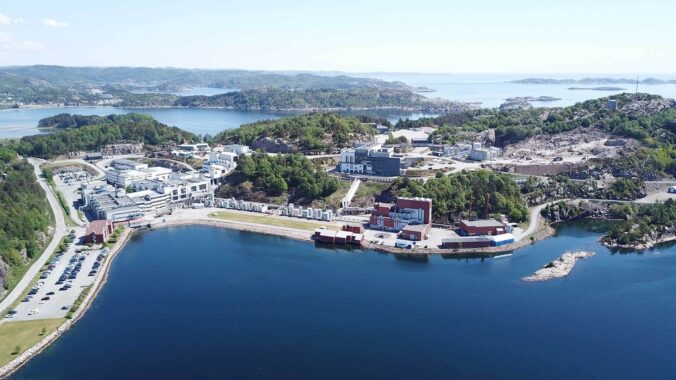
We recently spent some time talking with technical engineer Odd Skagestad from GE Healthcare Lindesnes about how DeltaV-Seal™ technology has impacted operations at a world-leading pharmaceutical…
Pipeotech’s reach goes atomic
Geir Otto Amundsen on Case Studies · Jan 05, 2021
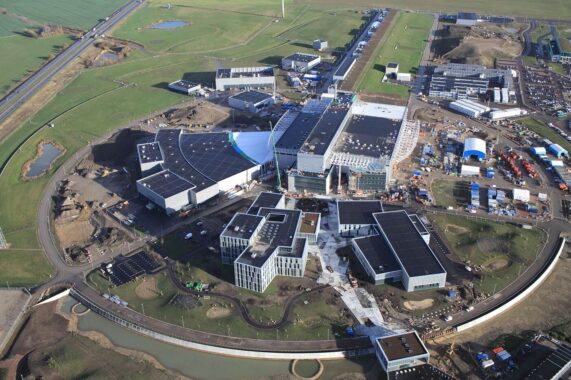
Pipeotech has taken gasket tightness to new microscopic levels by supplying DeltaV-Seal™ to European Spallation Source, the world’s most powerful neutron source, in Lund, Sweden. The new research…
VARD finds the perfect fit

Jo Shailes on Case Studies · Nov 11, 2020
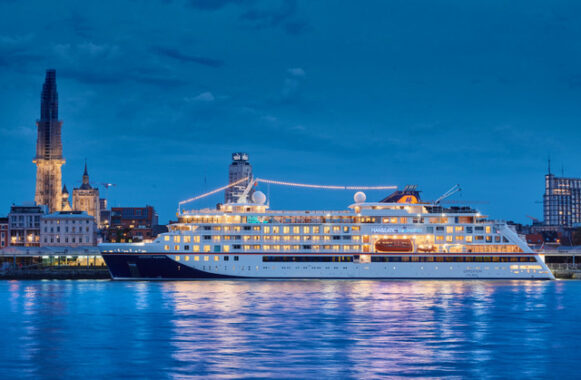
Norwegian-based shipbuilder VARD has been installing Pipeotech’s DeltaV-Seal™ in its vessels since 2016 and the cost-saving benefits have been very clear to Johny Morland, Principal Engineer, QA and…
Corrosive influence - The dangers of galvanic corrosion for pipelines
Geir Otto Amundsen on Case Studies · Apr 22, 2020
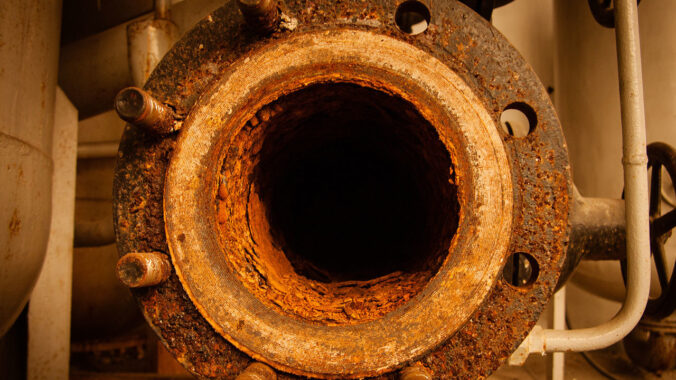
Prevention is always better than a cure. Avoiding issues in the first place, rather than attending to them once they’ve occurred, is plain common sense. So why do so many industrial facilities…
Pipeline safety – How gasket choices can mitigate health and safety risks
Geir Otto Amundsen on Case Studies · Jan 31, 2020
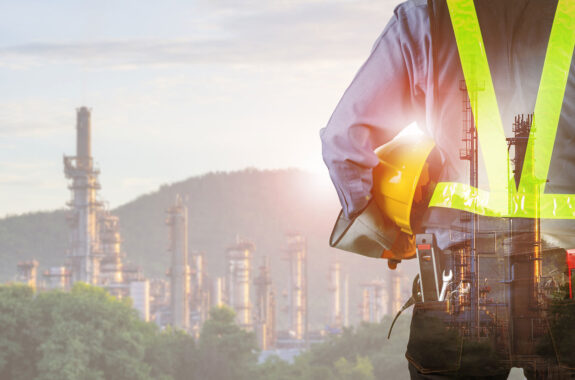
Nothing is as important as health and safety when it comes to industrial facilities. However, a critical component in piping systems is often overlooked, viewed as a consumable rather than a key to…
Stopping expensive leakages at historic brewing facility
Geir Otto Amundsen on Case Studies · Jan 31, 2020
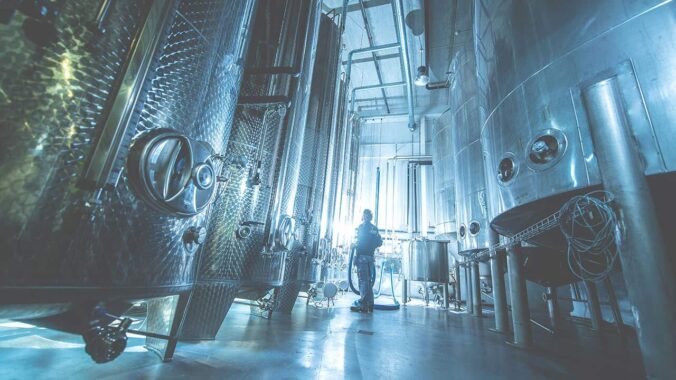
With the title of ‘the oldest brewery in Norway’, the Aass brewery is about as close as it gets to being a Norwegian institution. Situated on the banks of the river in the busy port city of Drammen…
DeltaV-Seal™ replaces kammprofile gaskets at critical distribution facility

Jo Shailes on Case Studies · Jun 12, 2019
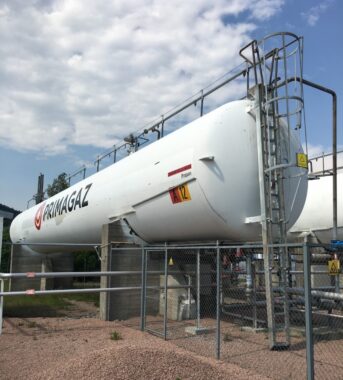
After a long relationship utilizing kammprofile gasket technology, Norwegian LPG distributor PrimaGaz Norge AS has decided to abandon the old kammprofile gasket design in favor of the new DeltaV-Seal…
Flare tip leakage is too hot to handle for the competition
James Knights on Case Studies · May 15, 2019
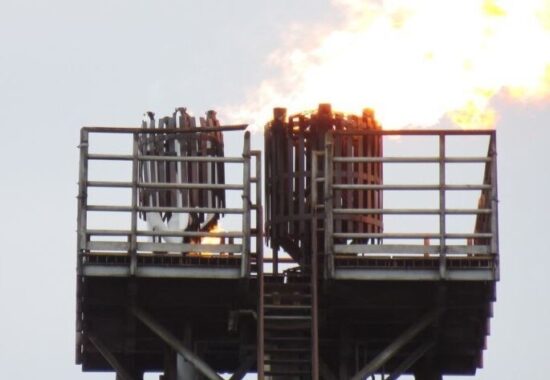
Pipeotech was called upon to provide a solution for Flare Tip flange leak in the North Sea. A North Sea Operator came to Pipeotech with a problem affecting a Flare line on their platform. This was…
Intergas exclusively use DeltaV-Seal™

Jo Shailes on Case Studies · Mar 26, 2019
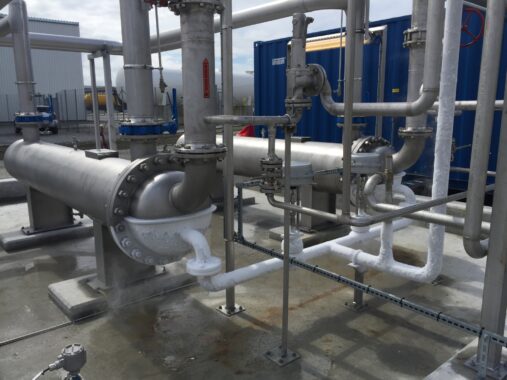
Following a highly successful test period, Intergas AS has announced that the DeltaV-Seal has been named as their exclusive seal of choice for all current and future liquefied natural gas operations.…